Project R.A.C.E.
Nell'ambito del "Project R.A.C.E." (Reaction Application for Composite Evolution), Hennecke insieme a top partner del settore ha compiuto un passo decisivo per lo sviluppo che già ora consente di produrre in pochi secondi complessi componenti cavi in materiale composito fibrorinforzato. Il cuore del progetto è rappresentato da una catena di processi per la produzione di un portatarga per moto in un materiale composito a base di fiber di carbonio in una struttura cava. Nella struttura tradizionale, il portatarga pesa oltre 765 grammi. Nell'ambito del "Project R.A.C.E.", il componente ha un peso complessivo di appena 265 grammi, a fronte di prestazioni migliori. Si tratta di una riduzione del peso superiore al 60%!
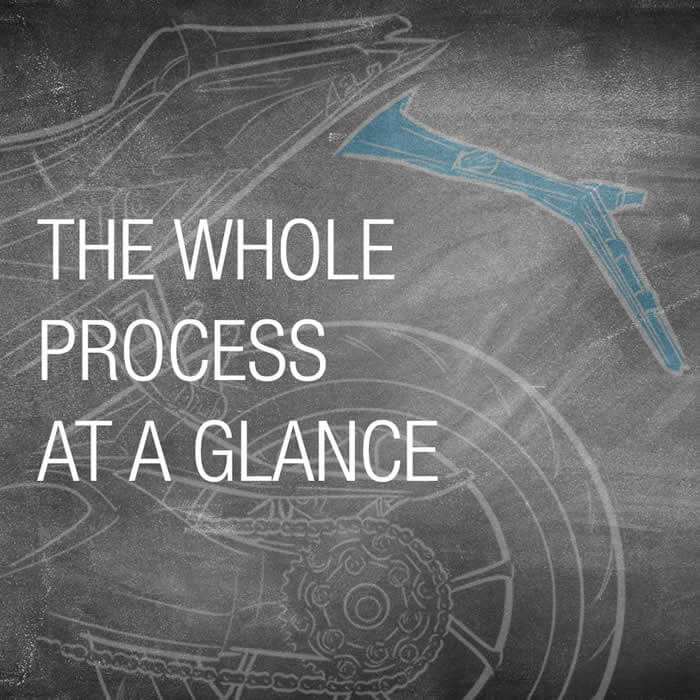
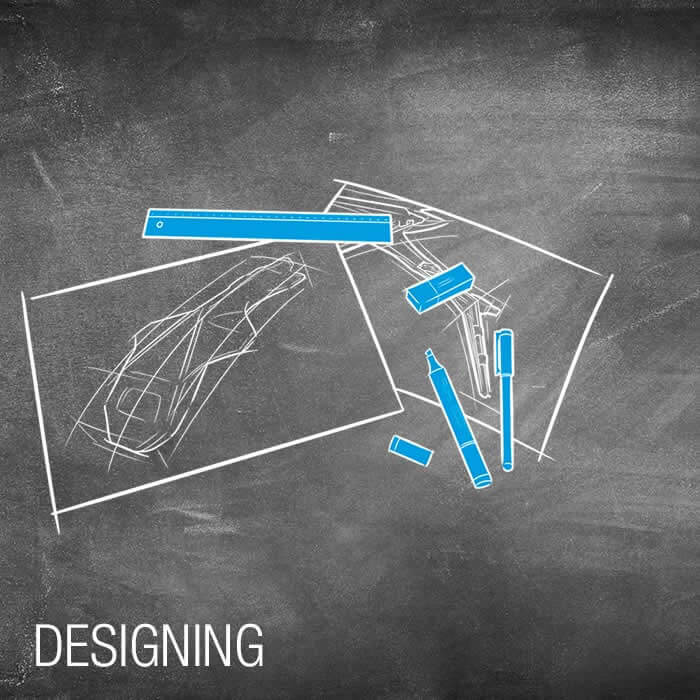
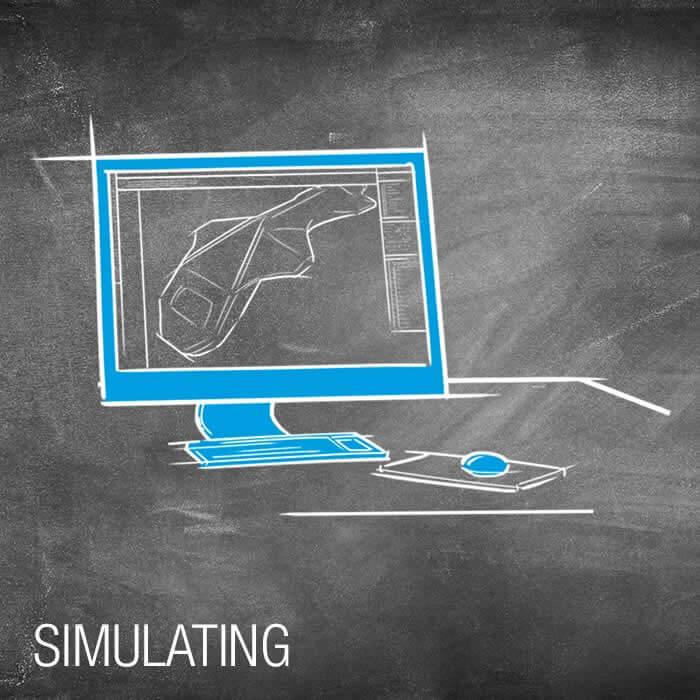
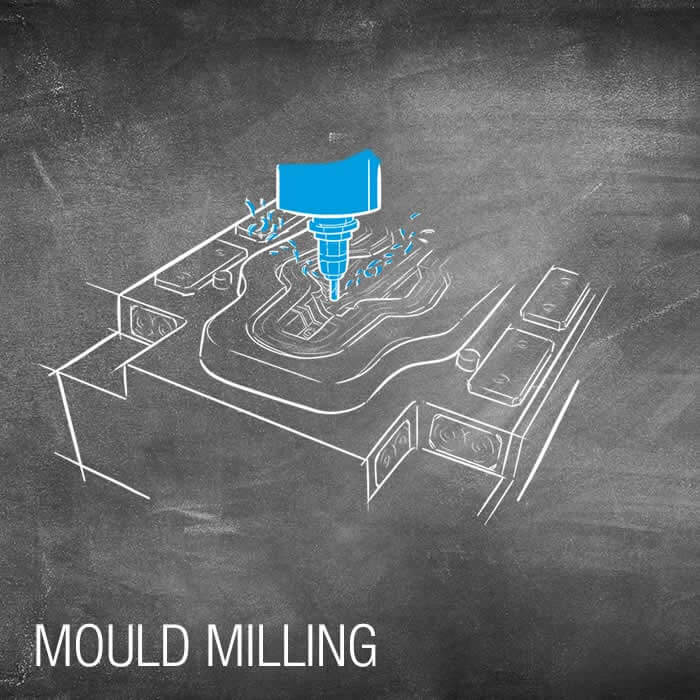
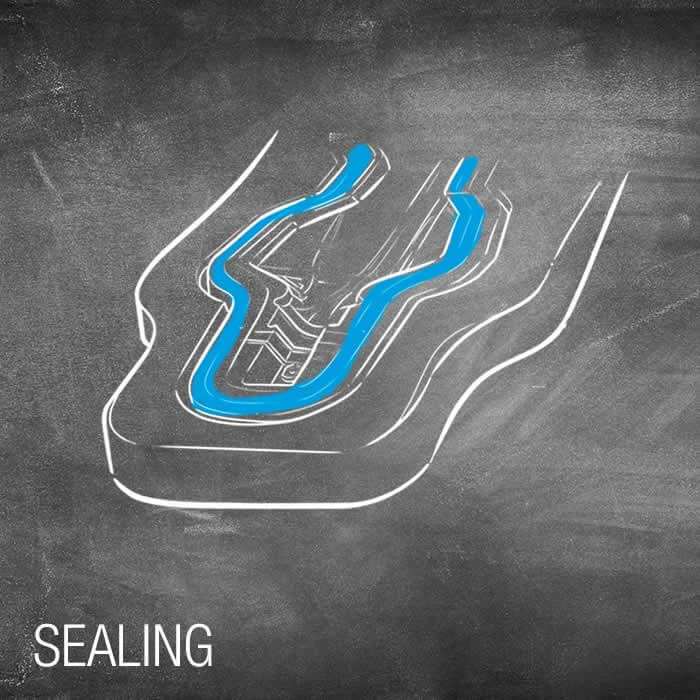
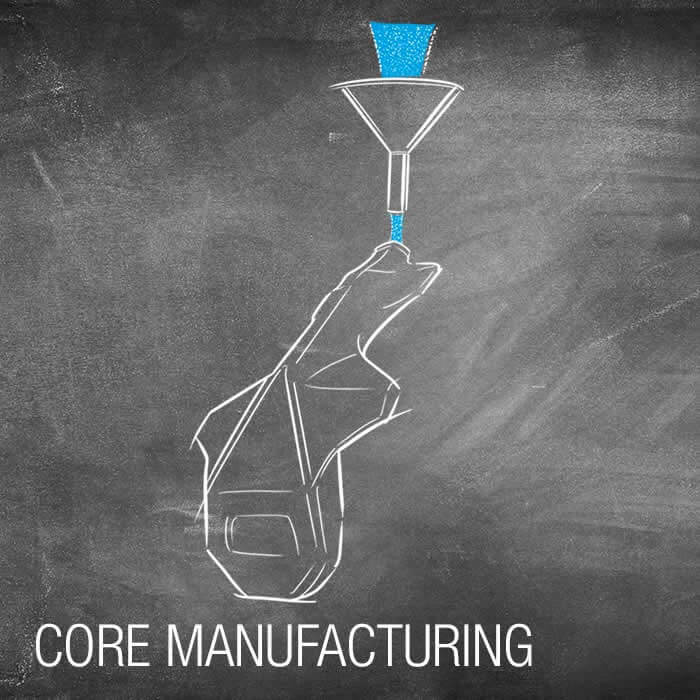
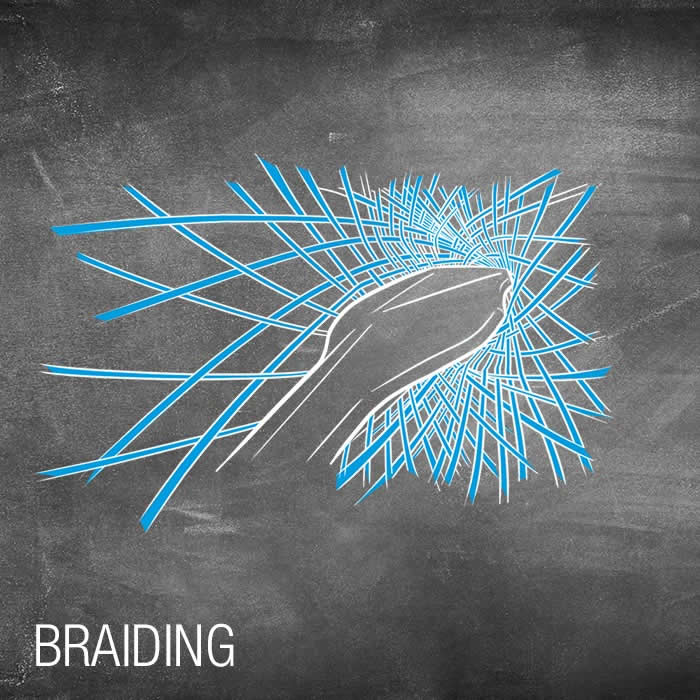
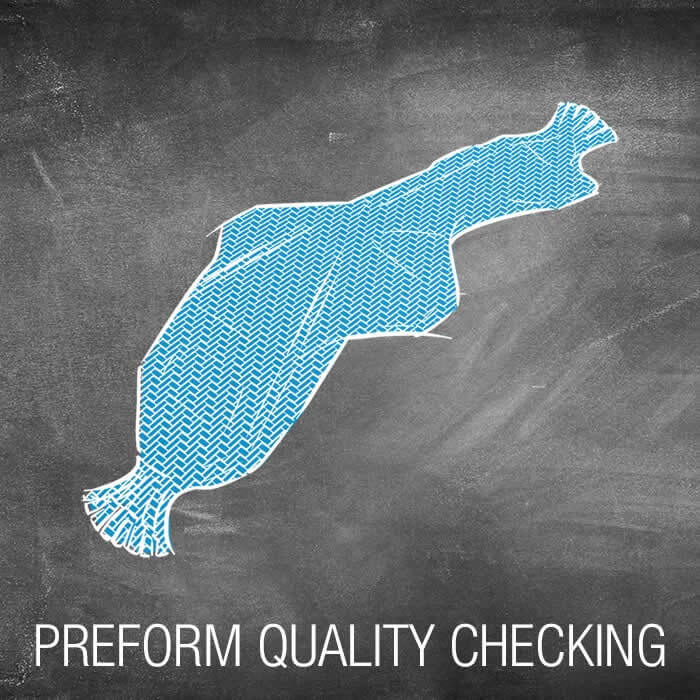
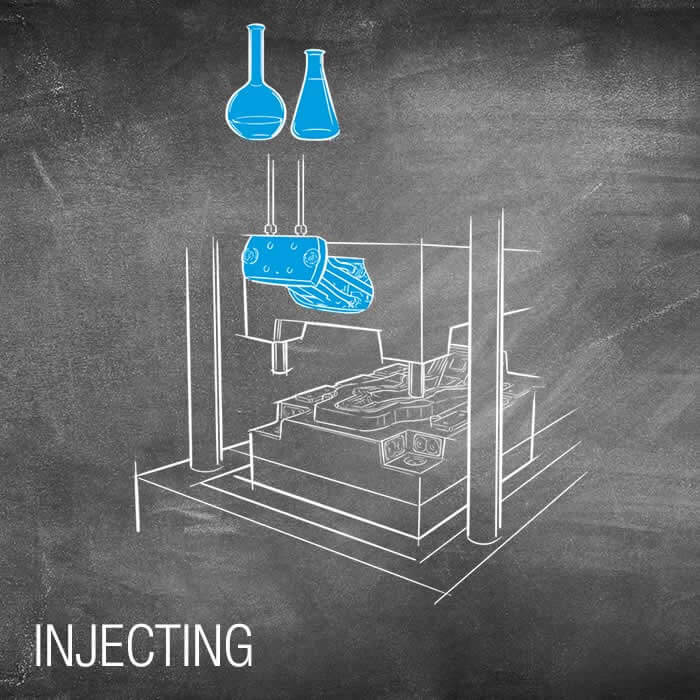
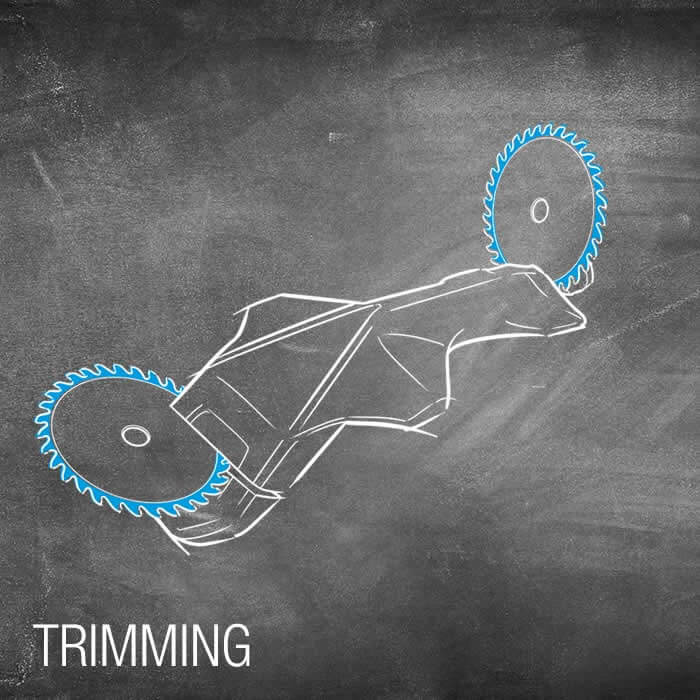
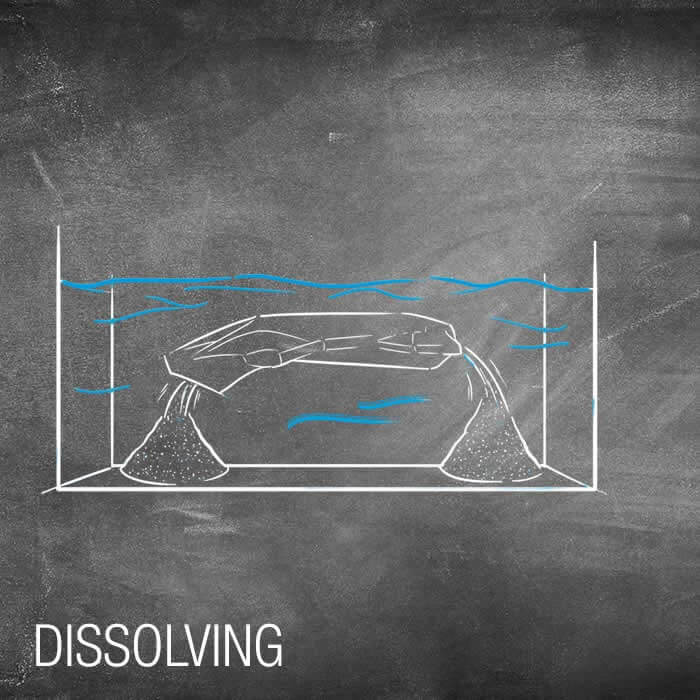
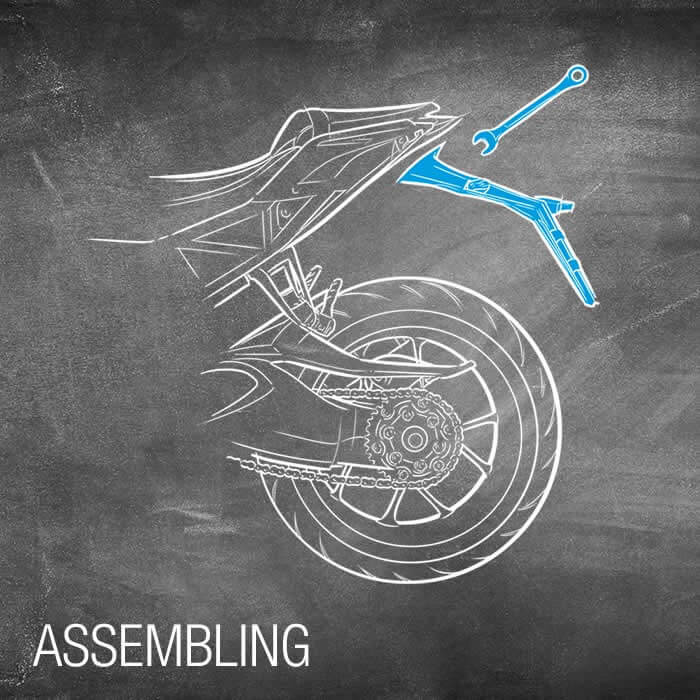
8 partner, 21 specialisti, 28 settimane di sviluppo
Le condizioni quadro del 'Project R.A.C.E.' sono state definite in modo chiaro
Il "Project R.A.C.E." è nato con la guida di Hennecke allo scopo di trasferire la nuova tecnologia di produzione CAVUS nella produzione di serie. Insieme ai partner Engel, Huntsman, Murtfeldt, IFB Stuttgart, Persico, Reinsicht (ex H2K Minerals) e KTM Technologies, è stato creato un team internazionale uniforme composto da 21 specialisti che si è impegnato a sviluppare un componente partendo da zero fino alla produzione in serie. È nato così il portatarga per la KTM 1290 SuperDuke R. La sfida per questo componente ad alte prestazioni è legata all'interazione della giusta progettazione con un design adatto alla produzione e alla fusione di processi efficienti basati sull'innovativa tecnologia CAVUS di KTM Technologies. CAVUS indica una catena di processi automatizzati per la produzione di complessi componenti cavi di tipo strutturale: dalla realizzazione del nucleo e dalla produzione dei prestampi in fiber di carbonio (per esempio, tecnologia a intrecciatura) fino al distacco del materiale del nucleo, passando per il processo HP-RTM. In questo modo è possibile realizzare una serie di configurazioni per quanto riguarda design e funzione.
L'interazione di design e ingegneria costituisce la base di un componente di successo. I progettisti Kiska e gli esperti di KTM Technologies utilizzano l'approccio dell'"Inside Out Design" per il portatarga della SuperDuke. I primi disegni a mano sulla carta costituiscono la base per il processo di sviluppo, partito in parallelo. Aspetti come l'ingombro, la soluzione di collegamento e la producibilità vengono tenuti in considerazione fin dall'inizio.
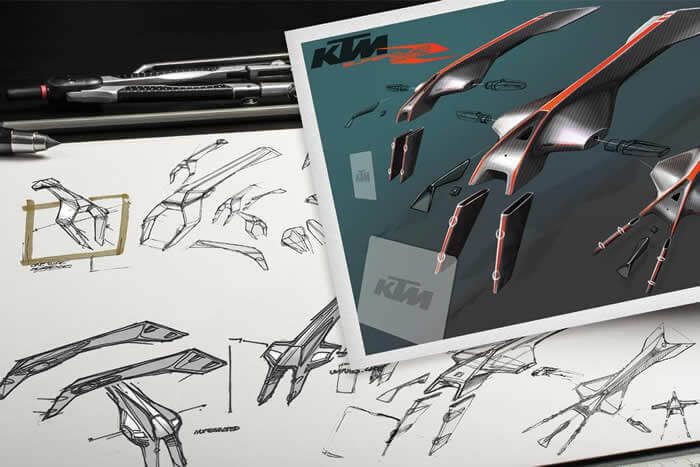
Per garantire la fattibilità del processo già in nelle prime fasi del progetto, gli ingegneri di IFB (Institut für Flugzeugbau, Istituto di costruzione aeronautica) dell'Università di Stoccarda hanno utilizzato diversi strumenti di simulazione. Dopo aver trasferito i primi schizzi nel software CAD, vengono fatte le simulazioni strutturali del componente, che ha fornito la prima stima del numero di processi di intrecciatura necessari. Questi risultati vengono utilizzati nella prima fase della simulazione dell'intrecciatura, che ha fornito informazioni sull'angolazione delle fiber e sulle possibili zone problematiche.
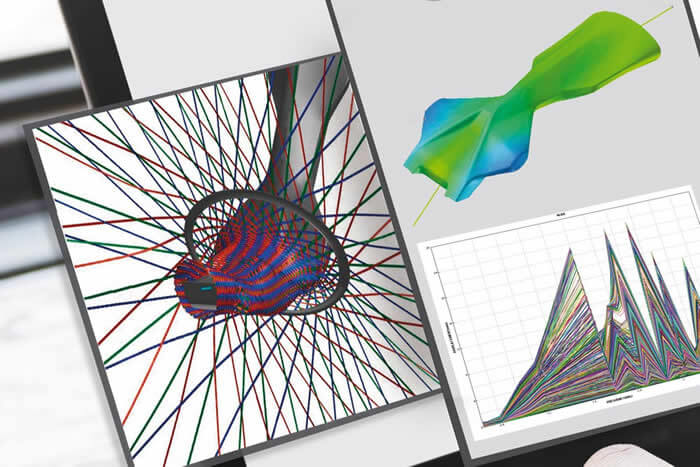
La parte centrale della tecnologia CAVUS è il nucleo in sabbia di Reinsicht (ex H2K Minerals). Per il "Project R.A.C.E.", il nucleo è stato messo a punto affinché resista a una temperatura di 330 °C e a una pressione di 500 bar. Il nucleo mostra le sue caratteristiche peculiari anche dopo l'infiltrazione dell'intrecciatura con la matrice. Il distacco dal componente viene effettuato con acqua pulita, senza grande dispendio energetico. Inoltre, la soluzione che ne deriva non è tossica. Grazie alla separazione indipendente dei componenti del nucleo, i componenti possono essere separati e riciclati in tutta semplicità. Così fino al 98% del nucleo è riutilizzabile, a seconda della combinazione di materiali.
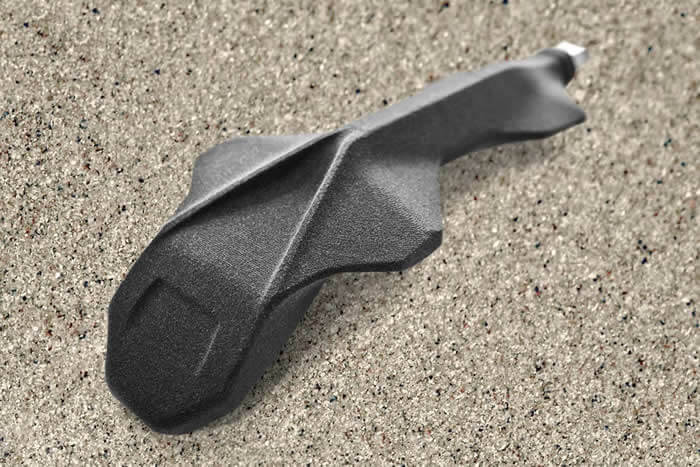
L'applicazione di fiber è stata effettuata dall'Istituto di costruzione aeronautiva dell'Università di Stoccarda tramite alla tecnologia di intrecciatura. A questo proposito, il nucleo è stato fissato in un dispositivo di serraggio sul robot dell'impianto di intrecciatura e fatto passare attraverso una ruota di intrecciatura sulla base del percorso calcolato nella simulazione. Per il "Project R.A.C.E." è stato utilizzato un intrecciatore radiale Herzog RF 1/64-100. Il tessuto viene applicato sul nucleo con 64 fili da intrecciare, composti da 24k roving in fiber di carbonio. Lo spessore dei denti sul fusello determina quanto l'intreccio è stretto sul nucleo. Una forza di trazione di 600 grammi dei denti ha dato i risultati migliori per la flessibilità e la resistenza per l'intreccio biassale.
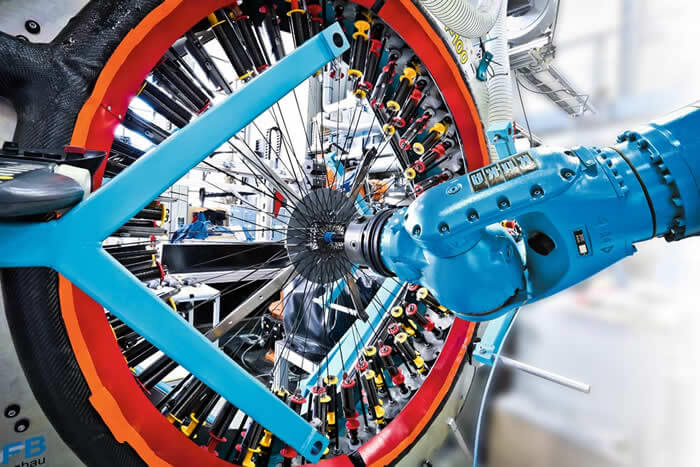
Il sistema a base di poliuretano VITROX® RTM 332 di Huntsman, utilizzato per il portatarga della SuperDuke 1290R, si contraddistingue per le incredibili proprietà meccaniche e l'eccellente lavorabilità. L'elevata resistenza all'urto e l'elasticità del materiale soddisfano i requisiti del componente. Importanti per il processo HP-RTM sono soprattutto le caratteristiche di lavorazione, perché il tempo di ciclo è fondamentale per la produzione in serie. Con un tempo "snap-cure" regolabile che va da meno di 30 secondi a 24 ore, con VITROX® è quindi possibile realizzare anche tempi di ciclo estremamente brevi.
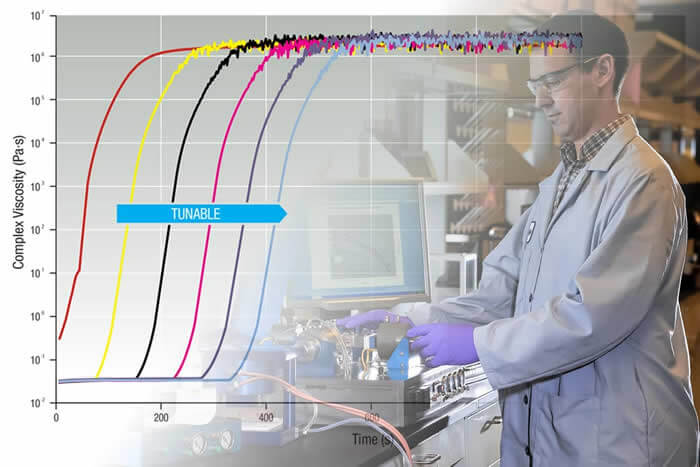
In particolare la qualità elevata e costante del componente è un argomento fondamentale che parla a favore dell'adozione del procedimento HP-RTM. Nel "Project R.A.C.E.", l'impianto è costituito da una macchina dosatrice Hennecke del tipo STREAMLINE e da una pressa a chiusura verticale del tipo Engel elast 400V compact. Grazie all'intensa collaborazione di Engel e Hennecke è possibile gestire l'intero processo tramite un impianto. Nell'impianto di dosaggio STREAMLINE vengono lavorati due componenti: poliolio e isocianato. Grazie alla regolazione della temperatura dell'intero impianto (incl. i pacchetti di flessibili), è garantita una temperatura costante attraverso il ricircolo dei componenti. Tramite una terza fune è inoltre possibile iniettare un agente distaccante omogeneizzato.
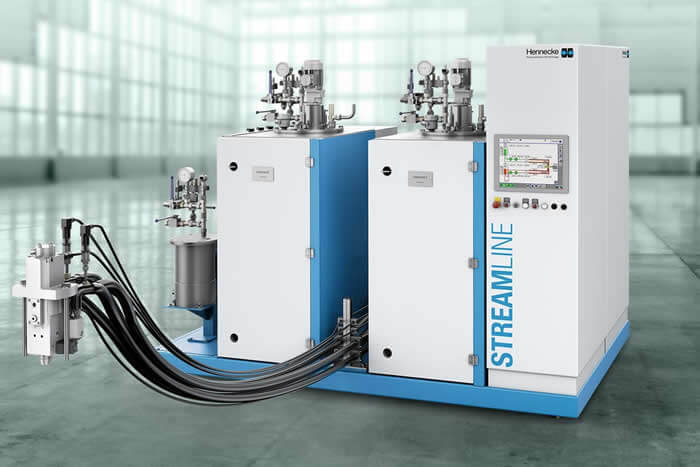
Per la miscelazione dei componenti, Hennecke punta sulla sua nuova testa di miscelazione MN10-3 RTM. Grazie al tubo di uscita conico con sensore pressione interna stampo, la testa di miscelazione ad alta pressione può essere impiegata anche per processi di aggancio semiautomatici. Per contrastare il restringimento dovuto alla polimerizzazione, lo stantuffo autopulente svolge inoltre la funzione di spingere idraulicamente in modo controllato la matrice durante l'indurimento. In questo modo è possibile ottenere superfici di ottima qualità. Un'altra particolarità della testa MN10-3 RTM è l'equipaggiamento di serie con gli ugelli a pressione costante brevettati. In questo modo si evita completamente il possibile impatto della pressione interna stampo sul processo di stampaggio dei componenti.
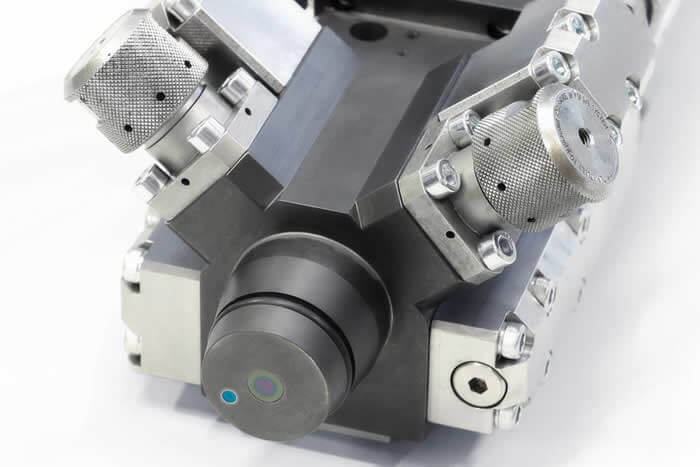
L'utilizzo di materiali plastici altamente reattivi con pressioni interne stampo fino al massimo a 200 bar risulta impegnativo a livello di tecnologia per gli stampi. Da un lato, lo stampo deve offrire tempi di stampatura elevati utilizzando fiber di carbonio abrasive e, dall'altro, deve garantire una superficie altamente lucida che rimane costante nel tempo. Grazie alle competenze dell'azienda costruttrice di stampi Persico di Nembro (Bergamo), è stato possibile venire incontro con successo alle esigenze del "Project R.A.C.E.". Con pressioni interne stampo medie pari all'incirca a 100 bar, anche l'impermeabilizzazione deve soddisfare requisiti elevati. Allo scopo è stato utilizzato un nuovo materiale di tenuta dell'azienda Murtfeldt. Murlock®, una plastica termoplastica, offre un'elevata azione impermeabilizzante per diverse centinaia di cicli di processo. Rispetto alle tradizionali guarnizioni a cordone rotondo, il materiale è resistente ai danni dovuti ai materiali residui o alle fiber di carbonio e, inoltre, è chimicamente inerte nei confronti dei sistemi di resine reattive.
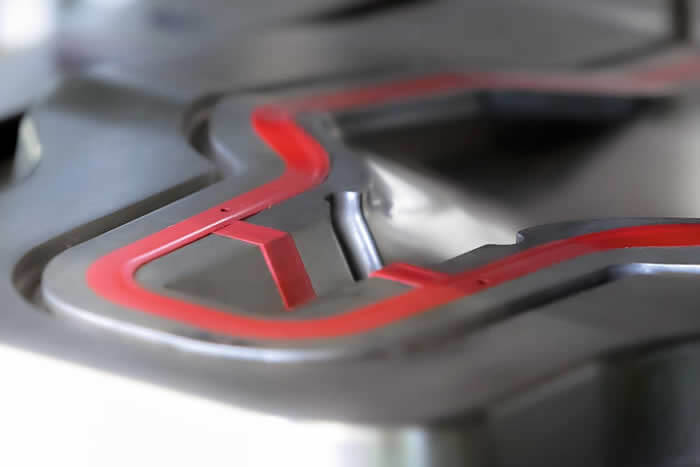
Il distacco del materiale del nucleo tramite acqua è una caratteristica peculiare della tecnologia CAVUS. L'aspetto particolare è che, nel processo, la sostenibilità è una priorità. Il nucleo può essere staccato dal componente senza l'uso di ulteriori solventi dannosi per l'ambiente. Dopo la separazione del componente sformato nei bordi di taglio, viene messo in un bagno d'acqua. La sabbia si deposita nella soluzione e può essere completamente riutilizzata per nuovi nuclei dopo l'essiccazione. Il legante che si trova nella soluzione può essere smaltito come acqua per usi industriali oppure essere addirittura utilizzato come fertilizzante nell'agricoltura. Dopo che la sabbia si è staccata dal componente, quest'ultimo può essere sottoposto alle normali fasi di postlavorazione dei componenti in compositi fibrorinforzati e quindi montati sul veicolo.
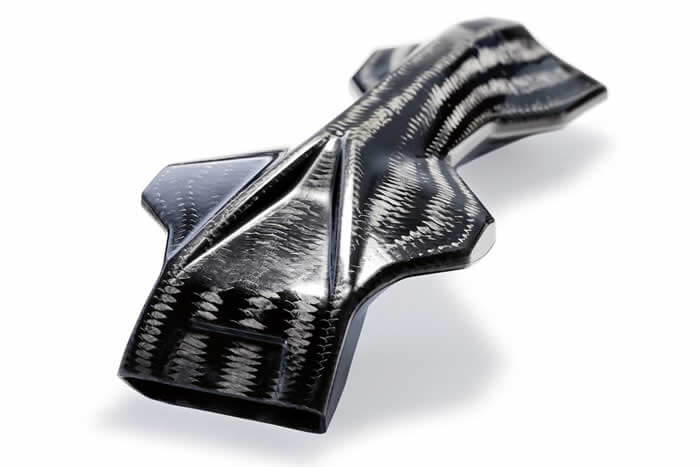
Project partner statements
Produzione dal vivo del componente alla K-Messe di Düsseldorf
Poco meno di 4000 visitatori sono stati ospiti dello stand Hennecke per vedere il processo. Un tempo di ciclo "part to part" di 125 secondi e una riduzione del peso superiore al 62% con una contemporanea valorizzazione del prodotto testimoniano il successo del progetto. Il "Project R.A.C.E." dimostra quindi in modo straordinario come è possibile raggiungere una fase di sviluppo decisiva nell'ambito della produzione in serie di componenti cavi in compositi fibrorinforzati sulla base della tecnologia CAVUS grazie all'impegno comune di partner altamente specializzati.
PROJECT R.A.C.E. “2.0”
Portataghe con struttura ibrida (GFRP/CFRP)
Il Project R.A.C.E. continua a svilupparsi. Il più recente approccio alla produzione è un portatarga con struttura ibrida, che garantisce la massima libertà di design a livello di forme e colori. La contornazione nel processo di intrecciatura viene effettuata con fiber di vetro. Grazie a un rinforzo mirato e, quindi, in funzione del caricamento mediante fiber di carbonio nella procedura Tailored Fiber Placement (TFP), l'utente riceve un componente che risulta altamente rigido, a fronte di un peso minimo e di costi sensibilmente ridotto delle materie prime. Una sigillatura ulteriormente ottimizzata del nucleo riduce inoltre il numero delle fasi necessarie, con un conseguente abbattimento dei costi di produzione. Il nuovo approccio alla produzione consente poi anche l'integrazione senza problemi di componenti elettronici come, per esempio, sensori o diodi luminosi.
Qui sono disponibili contenuti di accompagnamento in formato PDF
Per la valutazione è necessario Adobe Reader®, scaricabile gratuitamente qui.