Project R.A.C.E.
"Project R.A.C.E."(Reaction Application for Composite Evolution)의 일환으로 Hennecke는 업계 최고의 파트너들과 함께 복잡한 섬유 복합 중공 부품을 몇 초 만에 제조하는 것을 앞당길 수 있는 결정적인 개발 단계를 이루어냈습니다. 프로젝트의 중점은 탄소 섬유 합성 재료로 만든 모터사이클 번호판 홀더를 중공형 구조 설계로 제작하기 위한 프로세스 체인입니다. 기존 설계에서 번호판 홀더 무게는 765g이 넘었습니다. 그런데 성능까지 향상된 Project R.A.C.E. 부품의 전체 중량은 265g 밖에 되지 않습니다. 중량을 60% 이상 줄인 것입니다!
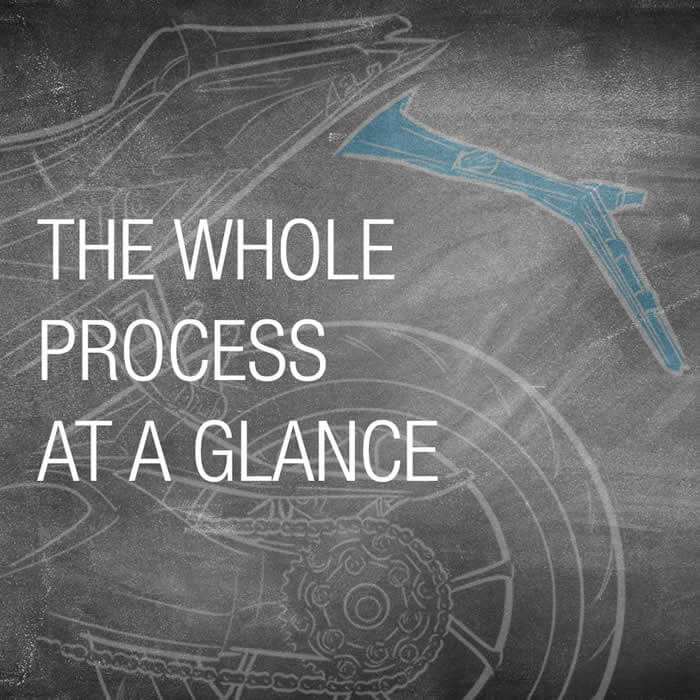
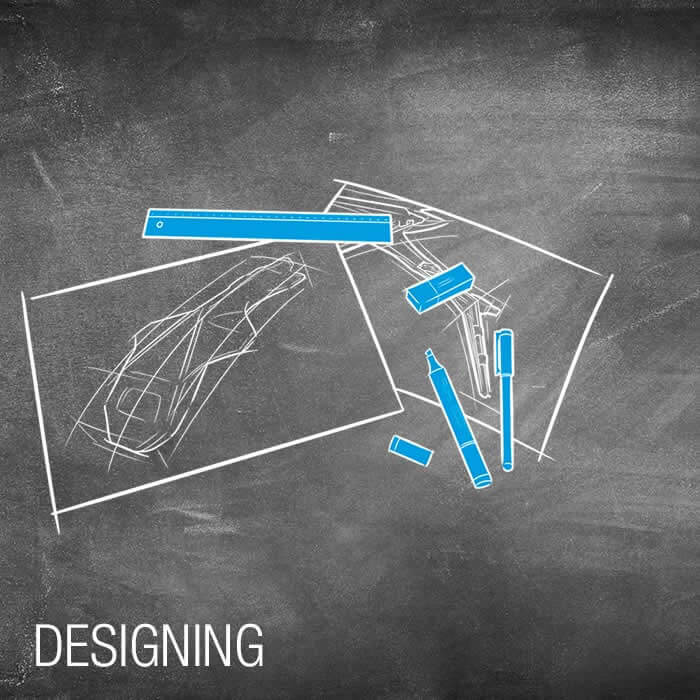
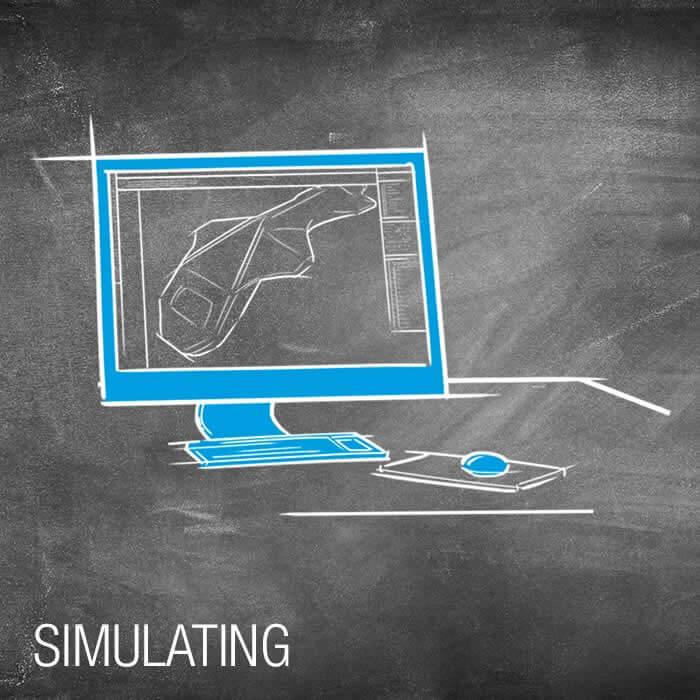
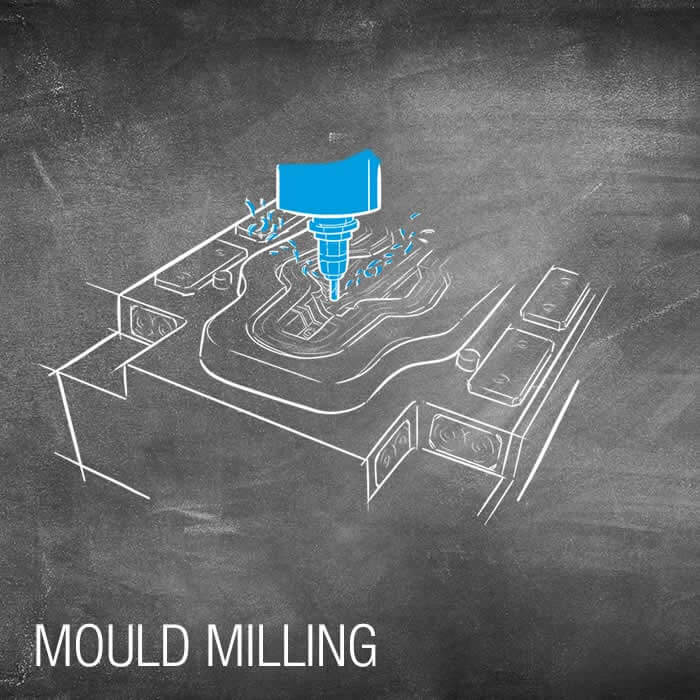
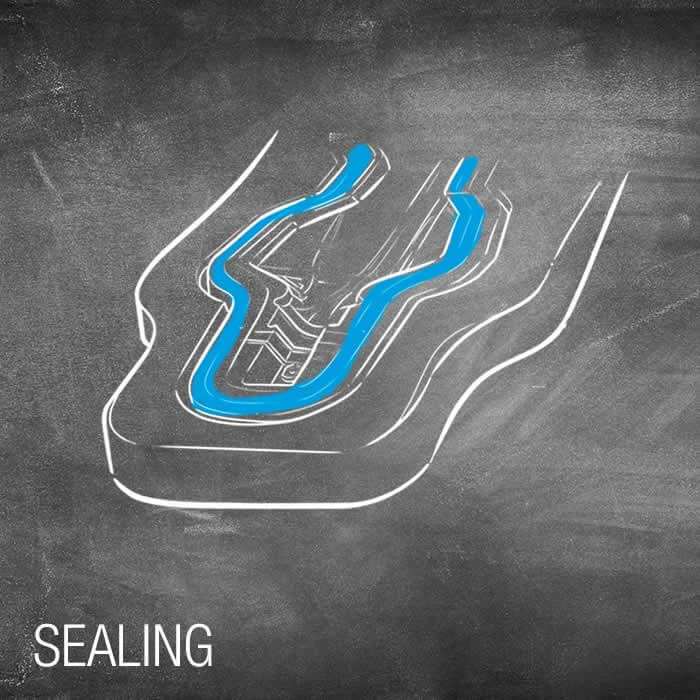
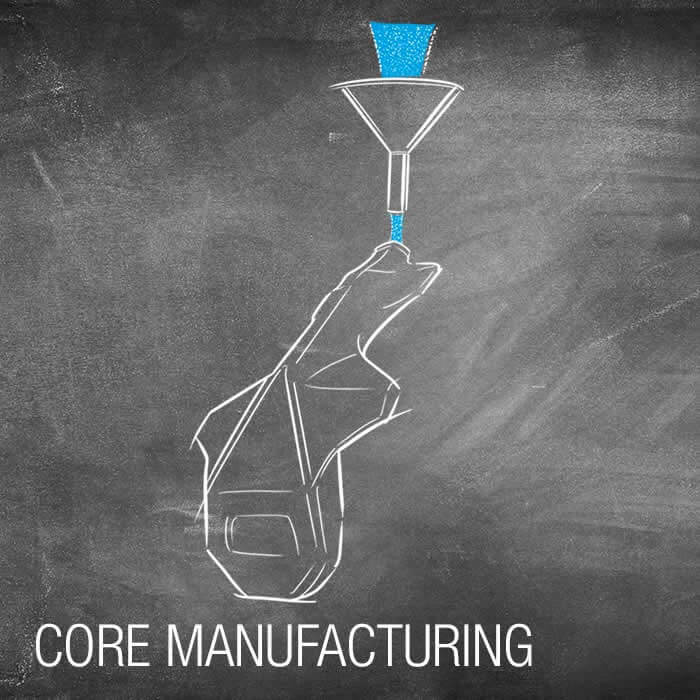
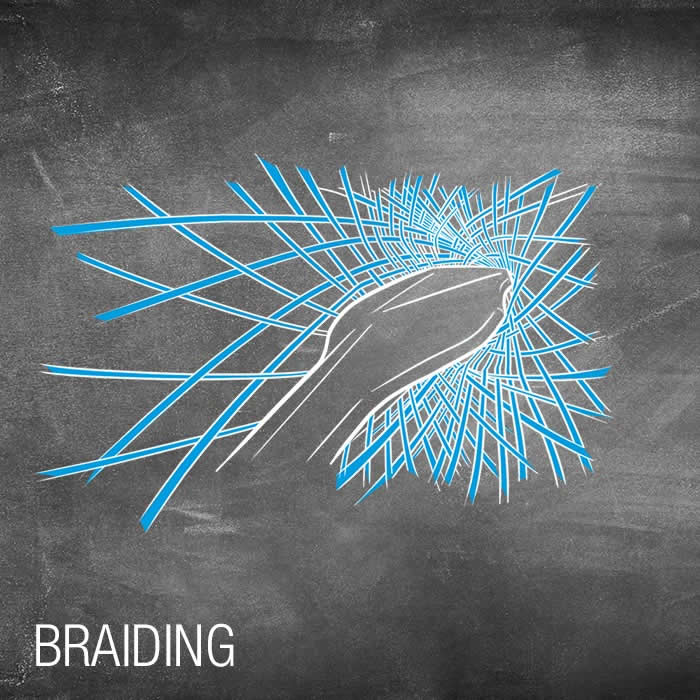
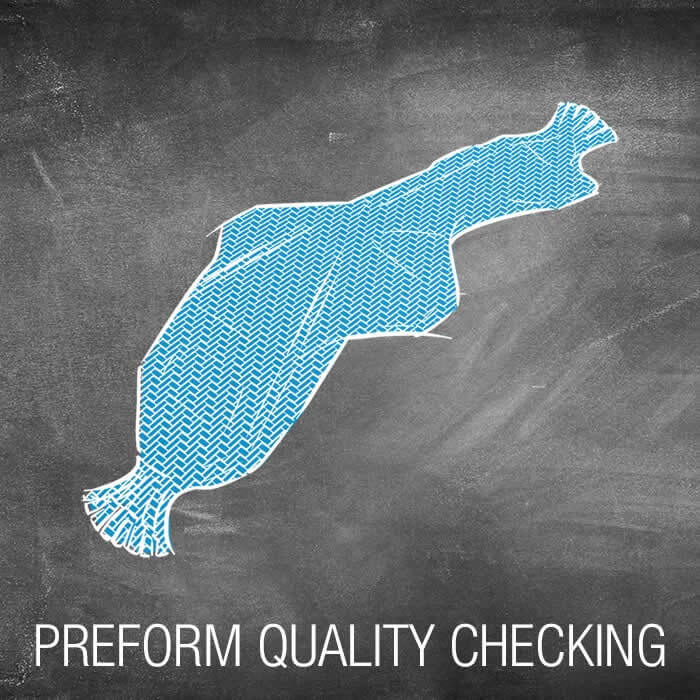
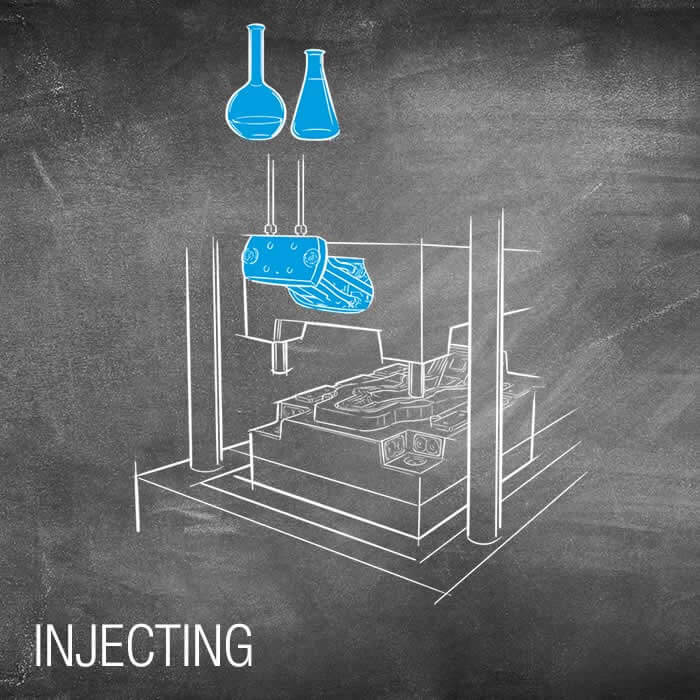
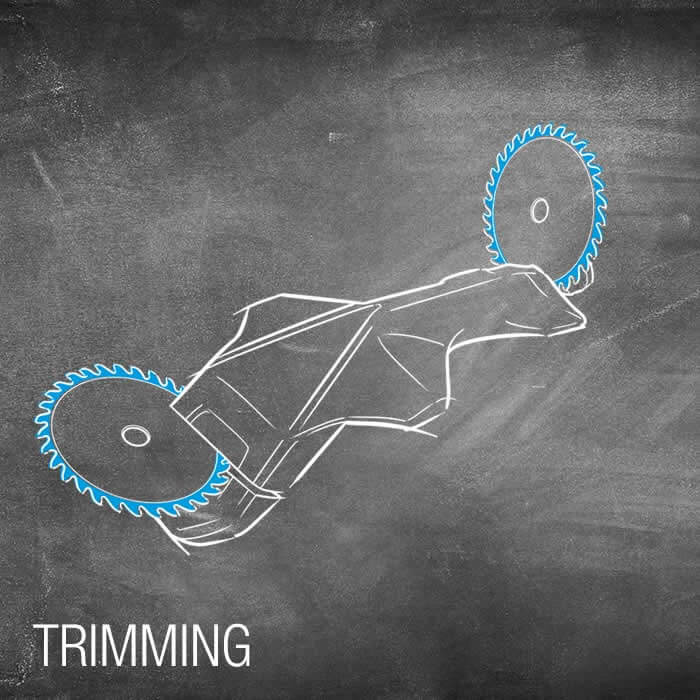
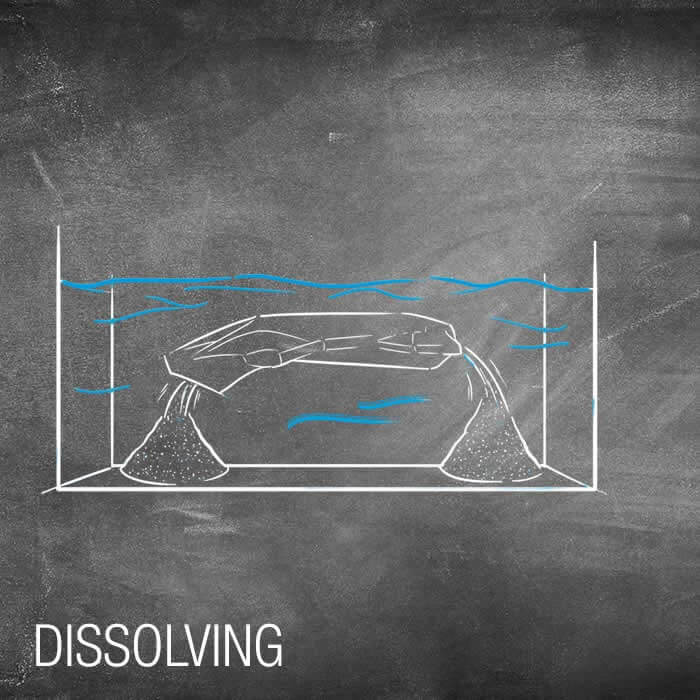
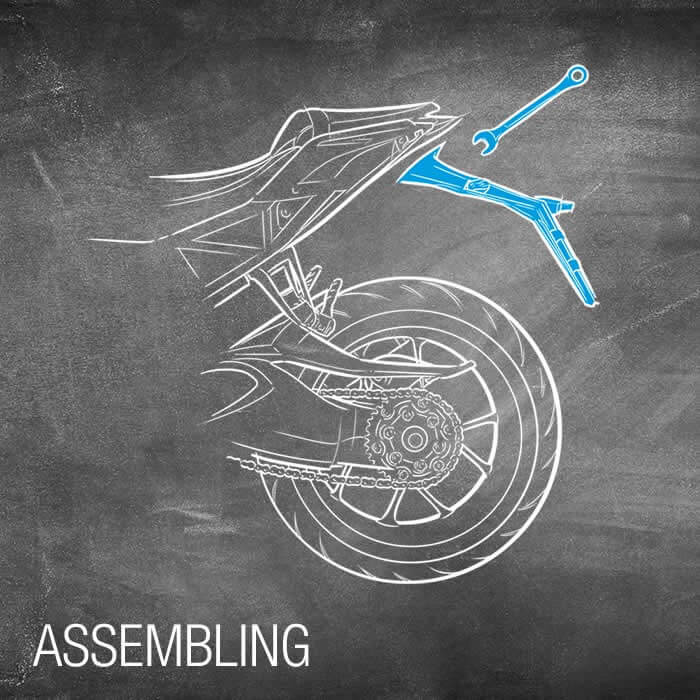
파트너사 8곳, 전문가 21명, 28주의 개발 기간
Project R.A.C.E.의 일반 조건은 명확하게 정의되었습니다.
Project R.A.C.E.는 새로운 CAVUS 생산 기술을 양산 프로세스에 접목하는 것을 목표로 Hennecke의 주도하에 시작되었습니다. 그렇게 파트너인 Engel, Huntsman, Murtfeldt, IFB Stuttgart, Persico, Reinsicht(전 H2K Minerals)와 함께 21명의 전문가로 구성된 전체적인 국제 작업팀이 형성되었고, 백지 상태에서 시작하여 양산 프로세스에 이르기까지: KTM 1290 Super Duke R용 번호판 홀더 부품을 개발하는 것을 과제로 설정하였습니다. 이 고성능 부품을 제작할 때 고심해야 할 것은 생산에 적합한 디자인과 KTM Technologies의 혁신적인 CAVUS 기술을 기반으로 한 효율적인 공정들을 결합한 올바른 설계가 상호작용할 수 있도록 만드는 것이었습니다. CAVUS는 코어 제조와 편조 같은 기술로 탄소 섬유를 사용한 프리폼 제조에서부터 HP-RTM 공정을 통해 코어 물질 방출에 이르기까지 구조적인 복잡한 중공형 부품 제조를 위해 자동화된 프로세스 체인을 나타내는 말입니다. 결과적으로 디자인과 기능 면에서 완전히 새로운 구성 가능성을 실현할 수 있습니다.
디자인과 엔지니어링의 상호작용은 성공적인 부품의 기반을 만듭니다. 여기서 Kiska의 디자이너와 KTM Technologies의 전문가는 Super Duke의 번호판 홀더에 "Inside Out Design" 접근법을 적용했습니다. 처음으로 종이 위에 그린 그림은 이와 동시에 시작되는 개발 프로세스의 기반을 형성합니다. 어셈블리 공간, 연결 컨셉 및 부품 제작 가능성 같은 측면은 시작부터 함께 고려합니다.
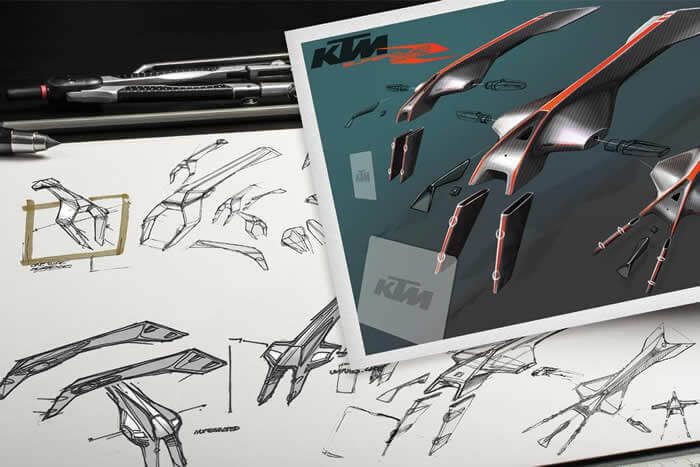
초기 프로젝트 단계부터 공정 능력을 확보하기 위해 슈투트가르트 대학교 IFB(비행건설 연구소)의 엔지니어는 시뮬레이션 도구를 사용합니다. 첫 스케치가 CAD 소프트웨어로 전송된 후에는 필요한 편조 작업 수의 첫 추정치를 산출하는 부품 구조 시뮬레이션이 실행됩니다. 이 결과는 섬유 각도 및 문제 발생 예상 구역에 대한 정보를 제공하는 시뮬레이션을 위한 다음 단계에서 사용합니다.
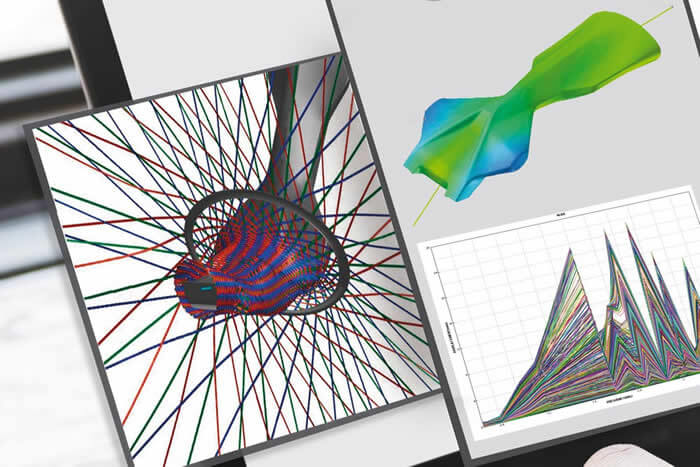
CAVUS의 핵심 구성요소는 Reinsicht(전 H2K Minerals)의 모레 코어입니다. Project R.A.C.E.에서 코어의 온도 저항은 330°C, 압력 저항은 500bar로 설정되어 있습니다. 코어의 특성은 매트릭스가 메시를 침투한 이후에도 나타납니다. 부품으로부터 방출하는 과정은 에너지 소비 증가 없이 순수한 물을 사용하여 이뤄집니다. 또한 여기서 발생하는 용제에는 독성이 없습니다. 핵심 부품을 직접 분리하면 구성 요소를 쉽게 분리하고 재활용할 수 있습니다. 이때 재료 조합에 따라 코어의 최대 98%를 재활용할 수 있습니다.
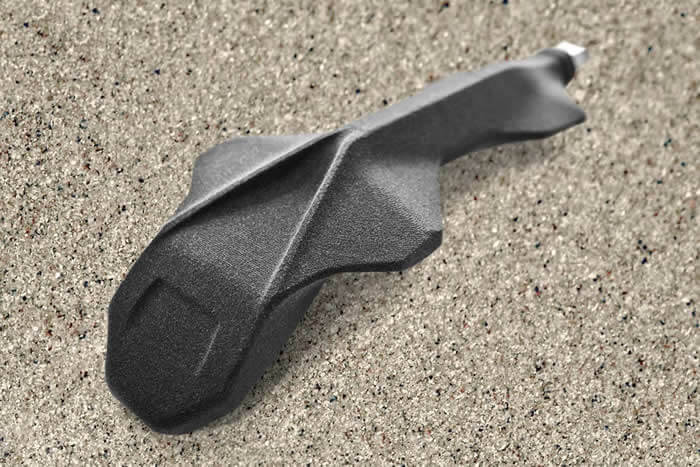
섬유 공급은 슈투트가르트 대학교 비행건설 연구소가 진행하였습니다. 이때 코어는 편조 시스템 로봇의 클램핑 장치에 고정되어 시뮬레이션에서 산출된 편조 경로를 따라 편조 휠을 통해 이동합니다. Project R.A.C.E.에서는 이를 위해 Herzog RF 1/64-100 레이디얼 편조기를 사용하였습니다. 24k의 플라스틱 섬유 로빙으로 구성된 편조 실 64개를 사용하여 텍스타일은 코어 위에 공급됩니다. 여기서 메시를 코어 위에 얼마나 단단히 고정하는지는 보빈의 스프링 강도에 따라 결정됩니다. 스프링 장력이 600g일 때 2축 편조 결과로 최상의 유연성과 강도를 갖춘 결과물을 공급하였습니다.
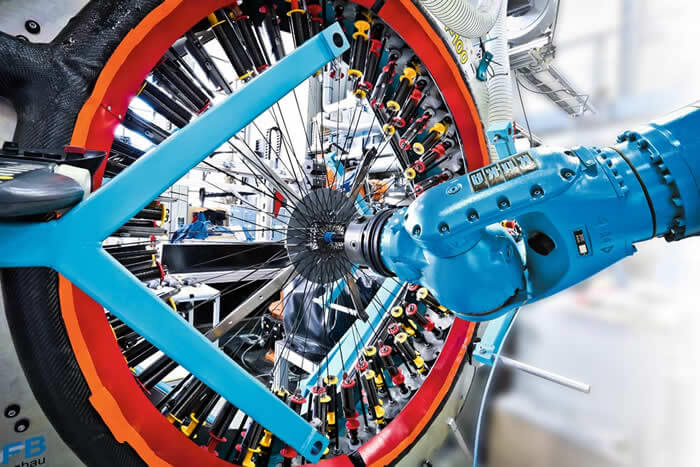
우수한 기계 특성 및 훌륭한 가공성이 Super Duke 1290R 번호판 홀더를 위해 사용한 Huntsman 폴리우레탄 시스템 VITROX® RTM 332의 특징입니다. 재료의 높은 충격 강도와 연성은 부품의 요구사항을 충족시킵니다. HP-RTM 프로세스에서 특히 중요한 점은 가공 속성인데, 양산 프로세스에서 사이클 시간이 중요하기 때문입니다. 따라서 30초 이하에서 24시간까지 설정 가능한 "snap-cure"를 사용하여 가장 짧은 사이클 시간까지 실현할 수 있습니다.
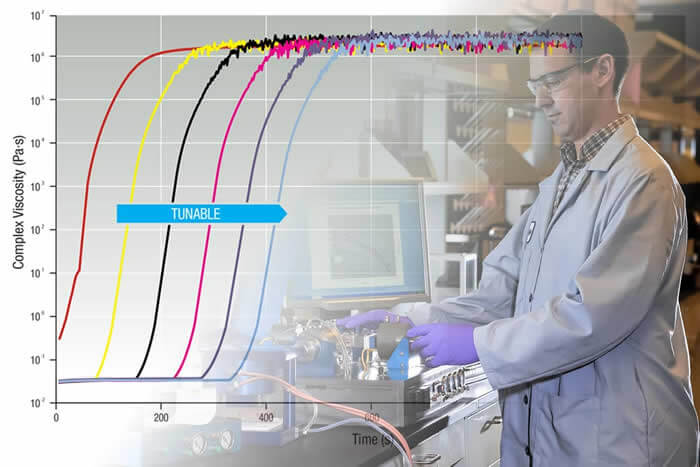
특히 높고 일정한 부품 품질은 HP-RTM 공정을 이용했다는 점을 결정적으로 보여줍니다. Project R.A.C.E.에서 시스템 셋업은 STREAMLINE 유형의 Hennecke 미터링 기계와 Engel elast 400V compact 유형의 수직 폐쇄 프레스로 구성됩니다. Engel사와 Hennecke의 집중적인 협업 덕분에 시스템 하나만을 이용하여 전체 공정을 제어할 수 있습니다. STREAMLINE 미터링 장치에서는 폴리올과 이소시아네이트 두 재료가 처리됩니다. 호스 패키지를 포함한 전체 시스템의 온도를 조절하여 재료가 재순환하면서 온도가 일정하게 유지됩니다. 또한 세 번째 가닥을 이용하여 균질화된 분리제를 주입할 수 있습니다.
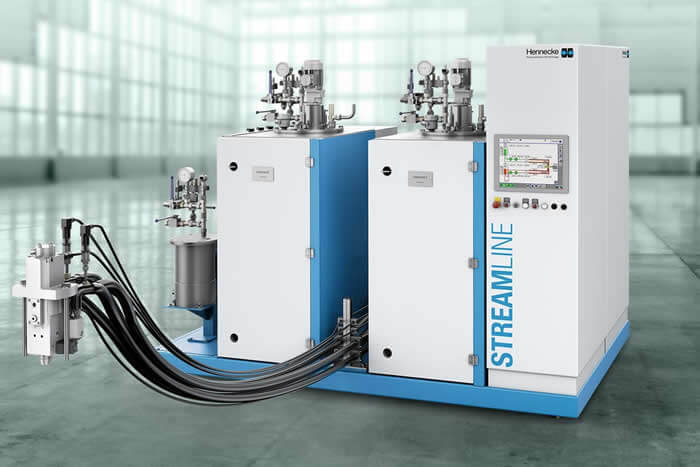
Hennecke는 재료 혼합에 새로 개발된 MN10-3 RTM 믹싱 헤드를 사용하고 있습니다. 통합형 캐비티 압력 센서가 있는 원뿔형 배출 파이프를 이용하면 반자동 도킹 작업에도 고압 믹싱 헤드를 사용할 수 있습니다. 또한 자체 세척 기능이 있는 플런저는 중합 반응 감소를 막기 위해 매트릭스가 최종경화하는 동안 유압식으로 제어할 수 있는 기능을 제공합니다. 그 결과 최고의 표면 품질을 달성할 수 있습니다. MN10-3 RTM의 또 다른 특징은 특허받은 정압 노즐이 기본 사양으로 장착되었다는 점입니다. 이로써 캐비티 압력이 부품의 압력 추이에 미칠 수 있는 영향을 완전히 방지합니다.
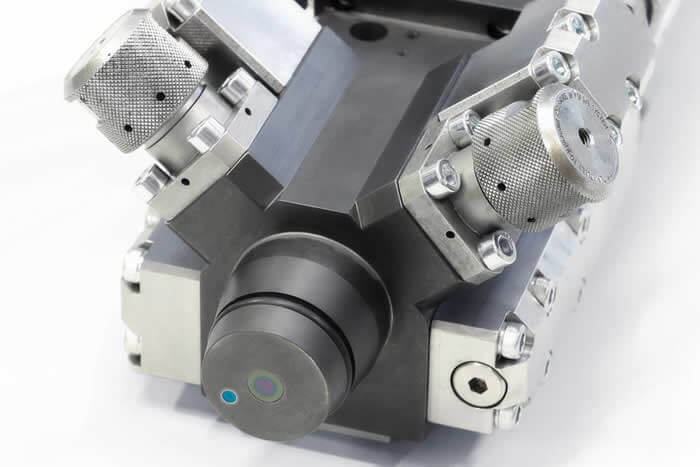
최대 200bar까지의 금형 내압에서 반응성이 높은 플라스틱을 사용하려면 높은 공구 기술 수준이 요구됩니다. 한편으로 연마성 탄소 섬유를 사용할 때 공구의 사용 수명이 길어야 하며, 다른 한편으로는 등속 회전식으로 고도 연마된 표면이 보장되어야 합니다. 이탈리아 넴브로(Nembro)의 공구 제조업체 Persico의 전문가들은 Project R.A.C.E.에서 이 요구사항을 성공적으로 구현하였습니다. 약 100bar의 평균 금형 내압에서는 실링도 높은 요구사항을 충족해야 합니다. 이를 위해 Murtfeldt사에서 개발한 새로운 유형의 실링 재료가 사용되었습니다. 열가소성 플라스틱인 Murlock®은 수백 개의 공정 사이클에서 최고의 실링 성능을 보장합니다. 기존의 실링 링을 이용한 실링과 비교했을 때 이 재료는 잔여 재료나 탄소 섬유로 인해 발생할 수 있는 손상에 내성이 강하고 이때 반응성 수지 시스템에도 화학적으로 영향을 받지 않습니다.
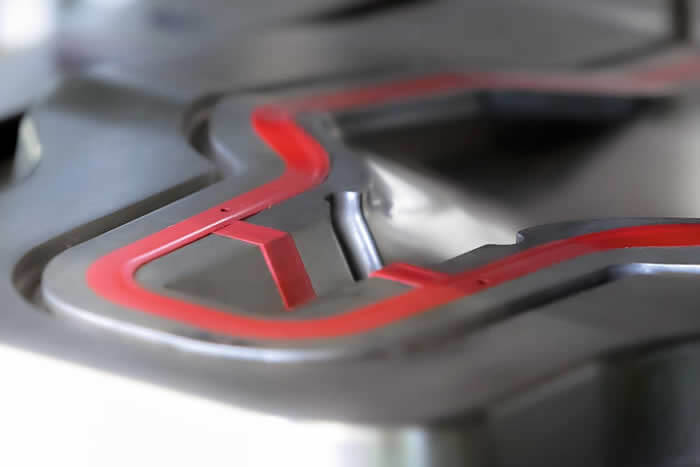
물을 사용하여 코어 물질을 방출하는 것은 CAVUS 기술의 특별 하이라이트입니다. 여기서 특별한 점은 지속 가능성이 최우선이라는 것입니다. 환경에 유해한 추가적인 용제가 없어도 코어를 부품에서 방출시킬 수 있습니다. 트리밍 엣지의 빠진 부품을 분리한 후 부품은 수조 위에 놓입니다. 모레는 용액에 침전하고 건조 후 새로운 코어를 위해 완전히 재사용할 수 있습니다. 용액에 포함된 결합제는 공정수로 폐기하거나 농업용 비료로 사용할 수도 있습니다. 모레가 부품에서 떨어지면 이를 차량에 장착되는 섬유 합성 부품의 일반적인 후처리 단계에 공급할 수 있습니다.
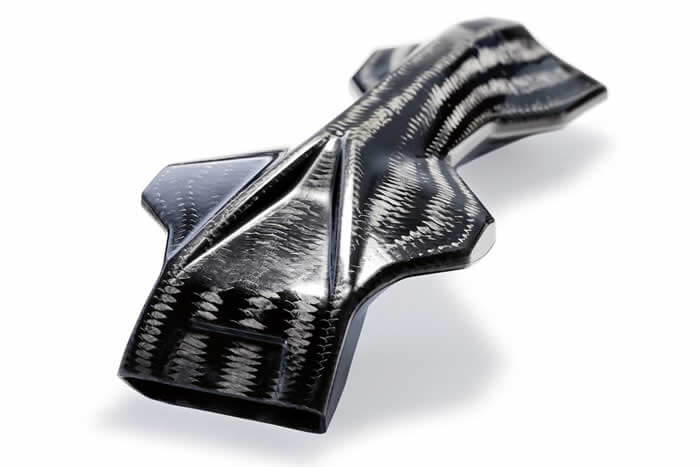
프로젝트 파트너의 성명서
PROJECT R.A.C.E. “2.0”
하이브리드 설계된 번호판 홀더(GFRP/CFRP)
Project R.A.C.E.는 끊임없이 발전하고 있습니다. 최신 제조 방식은 번호판 홀더를 하이브리드 설계하여 몰딩 및 컬러링 시 사실상 무한한 디자인의 자유를 최대한 보장합니다. 편조 공정의 컨투어링이 여기서는 유리 섬유로 실현됩니다. Tailored-Fibre-Placement(TFP) 공정에서 탄소 섬유를 사용한 목표에 따른 하중 기반 보강재를 활용하면 사용자는 최소한의 무게 및 상당한 원재료 비용 절감과 더불어 최대 강성값을 달성한 부품을 얻을 수 있습니다. 또한 한 번 더 개선된 코어 실링이 필요한 공정 단계 수를 줄여 제조 비용을 추가로 최소화합니다. 뿐만 아니라 새로운 제조 방식을 이용하면 센서장치나 발광 다이오드 같은 전자 부품도 쉽게 통합할 수 있습니다.
PDF 형식 문서를 보시려면 여기를 클릭해주세요.
PDF 자료를 보기위해서는 Adobe Reader를 여기에서 무료로 다운 받으실 수 있습니다.