Proyecto R.A.C.E.
En el marco del "Proyecto R.A.C.E." (Reaction Application for Composite Evolution), Hennecke, junto con los mejores socios del sector, tomó un paso decisivo para el desarrollo, el cual permite desde ahora fabricar en segundos componentes huecos de compuesto de fibra complejos. El proyecto se centra en una cadena de proceso para la fabricación de un soporte de matrícula para motocicletas de material compuesto de fibra de carbono en forma de construcción hueca. En la construcción tradicional, el soporte de matrícula pesa más de 765 gramos. En el marco del proyecto R.A.C.E., el componente presenta un peso total de solamente 265 gramos con un aumento de rendimiento. Esto constituye un ahorro de peso de más del 60 por ciento.
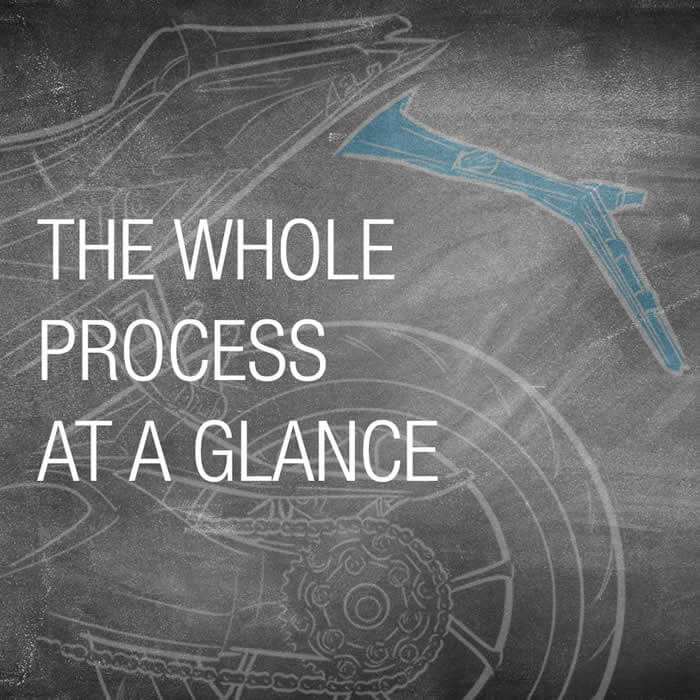
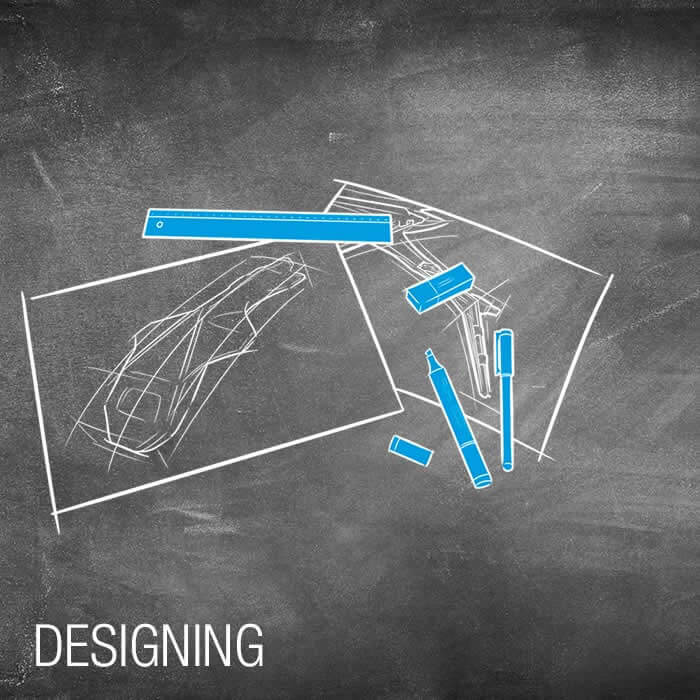
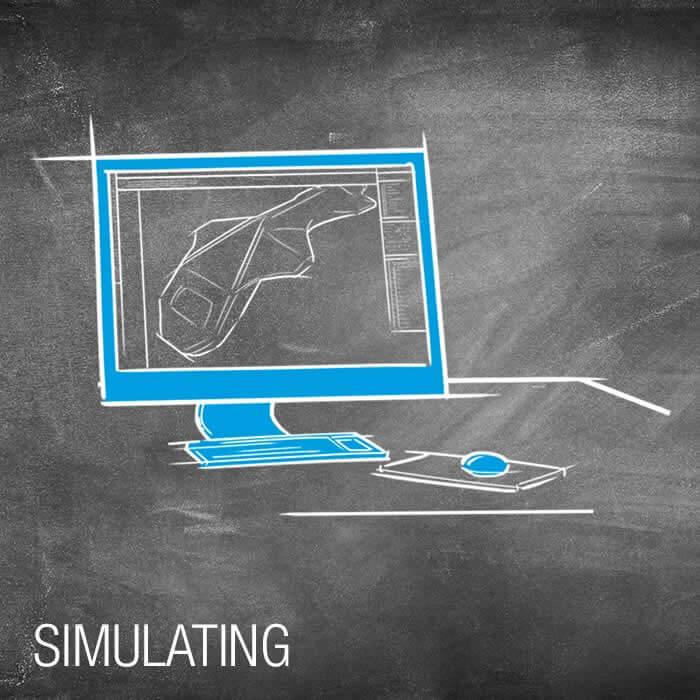
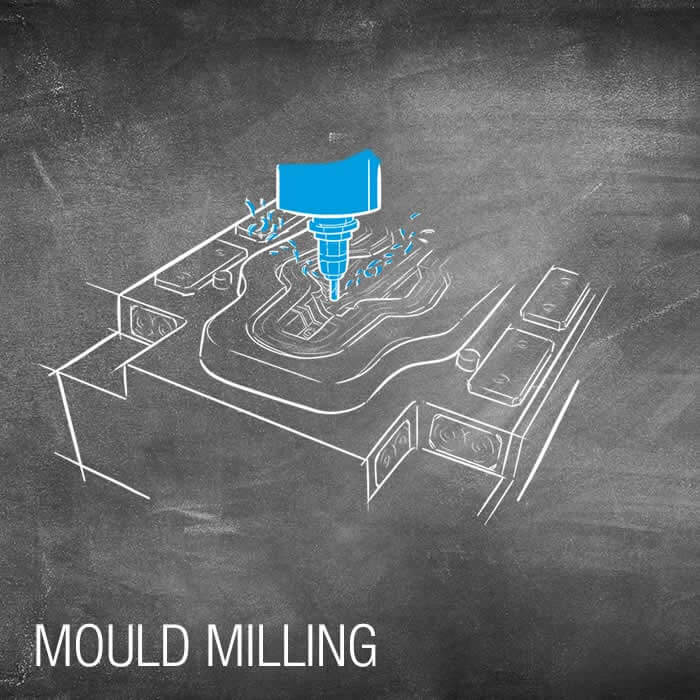
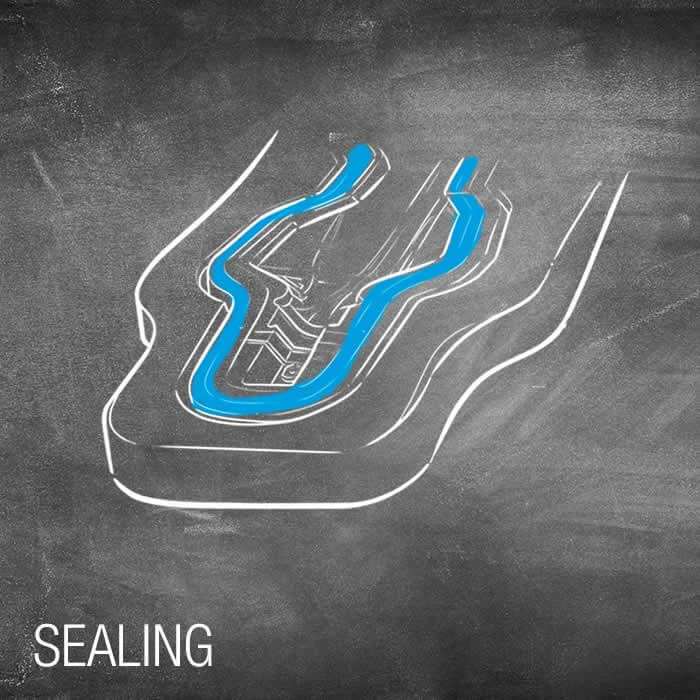
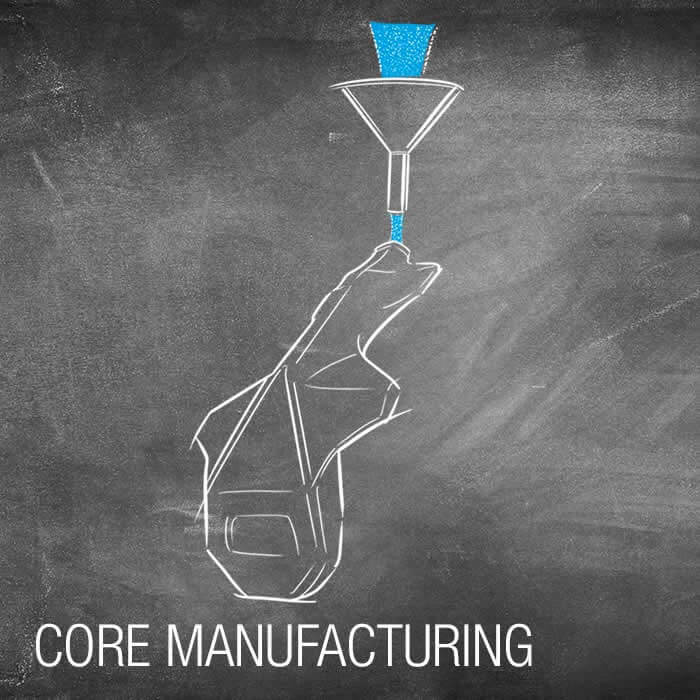
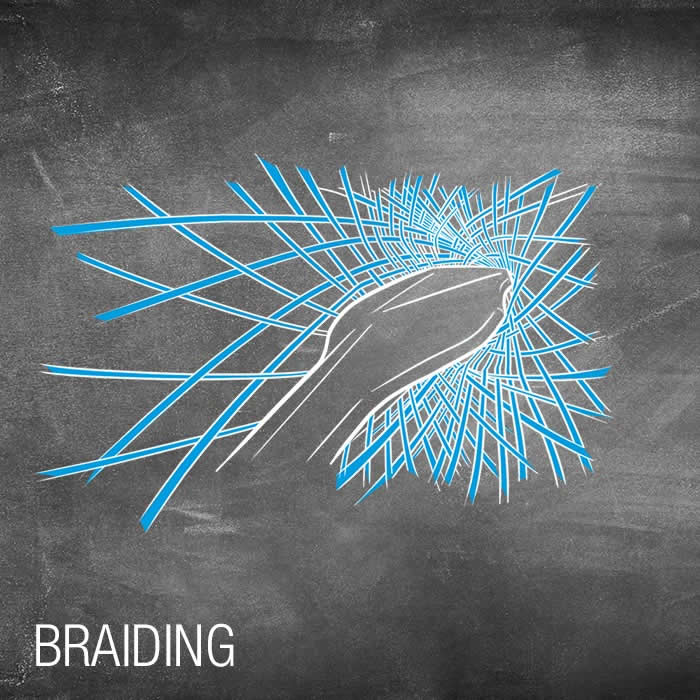
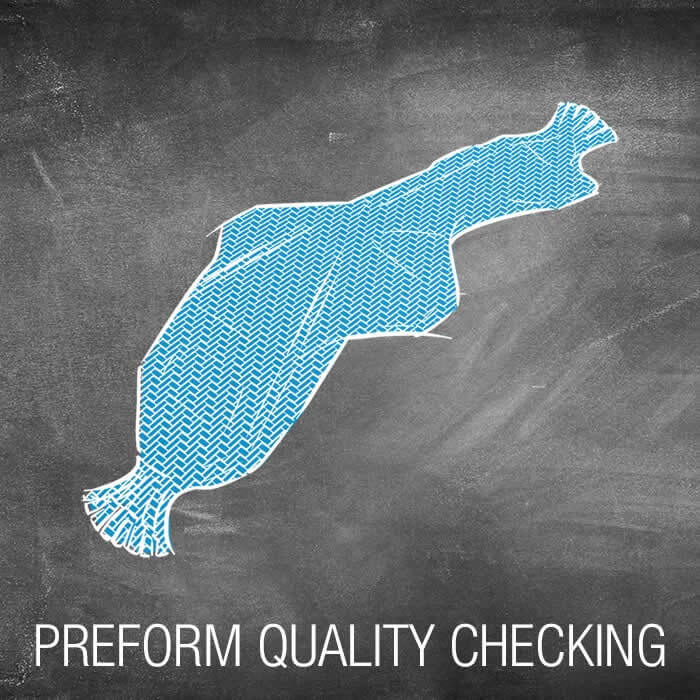
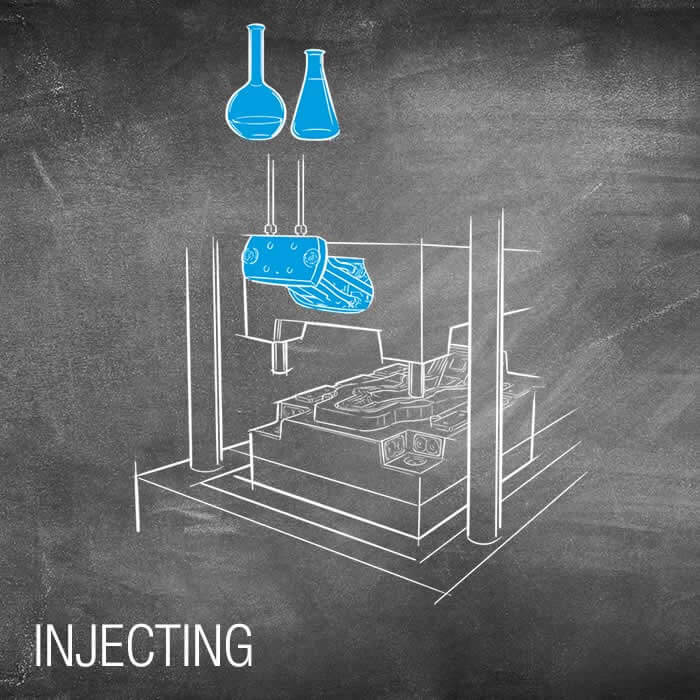
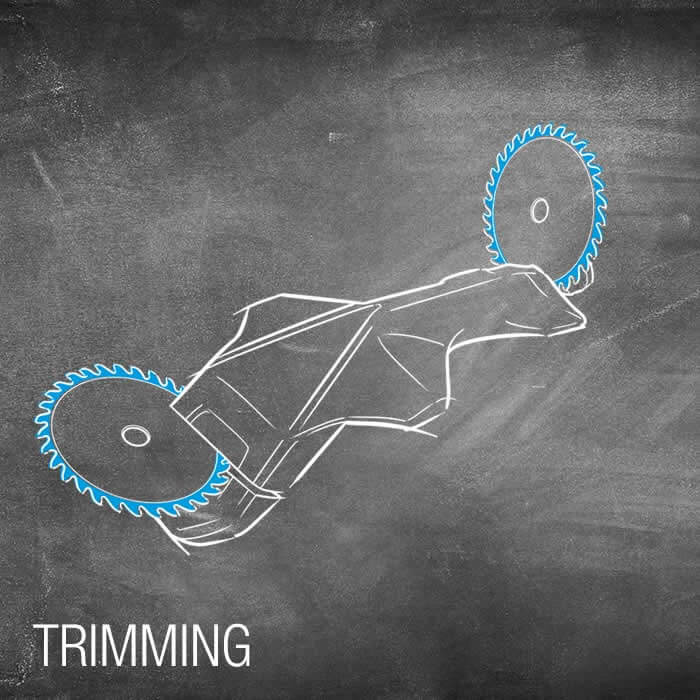
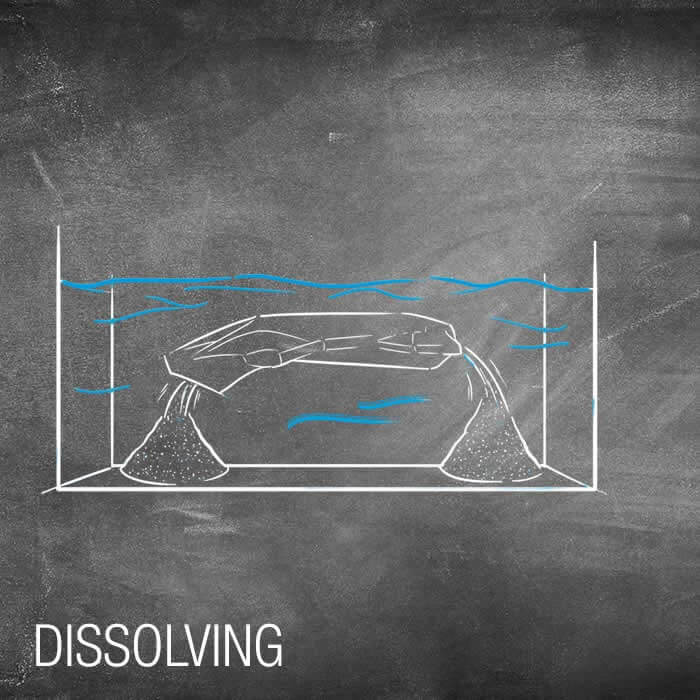
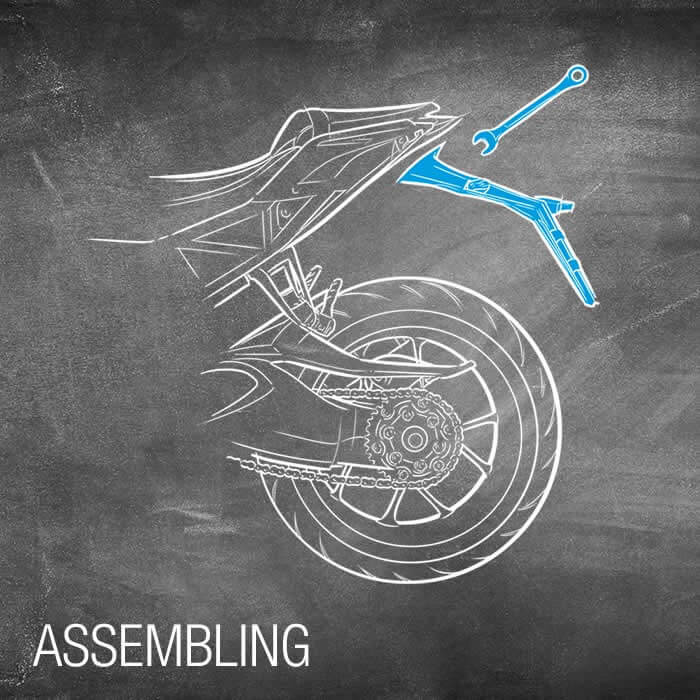
8 socios, 21 especialistas, 28 semanas de tiempo de desarrollo
Las condiciones marco del proyecto R.A.C.E. se definieron con claridad
Con el objetivo de transferir la nueva tecnología de producción CAVUS a la producción en serie, se creó el proyecto R.A.C.E. bajo la dirección de Hennecke. Junto con los socios Engel, Huntsman, Murtfeldt, IFB Stuttgart, Persico, Reinsicht (antes H2K Minerals) y KTM Technologies, se creó un eficiente equipo internacional de 21 especialistas cuya tarea era desarrollar un componente a partir de un papel en blanco hasta alcanzar la producción en serie: el soporte de matrícula para la motocicleta KTM 1290 Superduke R. El desafío para este componente de rendimiento yace en la interacción entre la construcción correcta y el diseño adecuado para la producción, así como la combinación del proceso efectivo sobre la base de la innovadora tecnología CAVUS de KTM Technologies. CAVUS describe la cadena de procesos automatizada para la fabricación de componentes huecos estructurales y complejos: desde la fabricación central y producción de moldes previos con fibras de carbono, por ejemplo en la tecnología de trenzado, hasta el proceso HP-RTM y la activación del material nuclear. Así, se pueden llevar a cabo posibilidades de diseño y función completamente nuevas.
La interacción de diseño e ingeniería crea la base para un componente exitoso. Por ello, los diseñadores de Kiska y expertos de KTM Technologies usan para el soporte de matrícula de la Superduke el enfoque de "Inside Out Design". Los primeros bocetos sobre papel crean la base para el proceso de desarrollo iniciado de forma paralela. Desde el principio se toman en cuenta diversos aspectos como el área de construcción, el concepto de conexión y factibilidad de producción del componente.
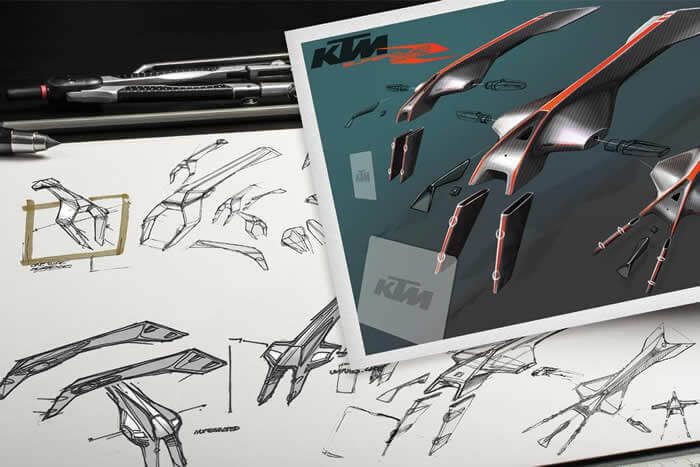
Para garantizar la capacidad del proceso ya en las primeras fases del proyecto, los ingenieros del IFB (Instituto de Construcción Aeronáutica) de la Universidad de Stuttgart utilizan diferentes herramientas de simulación. Después que se transmitieron los primeros bocetos en el software de CAD, se realizan las simulaciones de estructura del componente, que proporcionan una estimación inicial de la cantidad necesaria de procesos de trenzado. Estos resultados se usan en el próximo paso para la simulación de trenzado, que aporta información sobre el ángulo de fibra generado y sobre posibles áreas problemáticas.
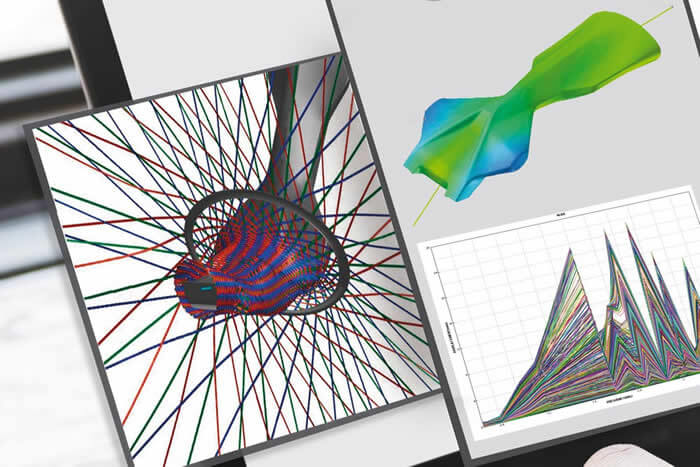
El núcleo de arena de Reinsicht (antes H2K Minerals) es un componente central de la tecnología CAVUS. Para el proyecto R.A.C.E. se ajustó el núcleo a una resistencia de temperatura de 330 °C y una resistencia de presión de 500 bar. Su particularidad muestra el núcleo también después de la infiltración del trenzado con la matriz. La separación del componente se realiza sin un aumento de energía con agua pura. Además, la solución que se genera no es tóxica. Gracias a la separación independiente de los componentes del núcleo, los componentes se pueden separar y reciclar con facilidad. De esta forma, se puede reciclar hasta el 98 por ciento del núcleo, en función de la combinación del material.
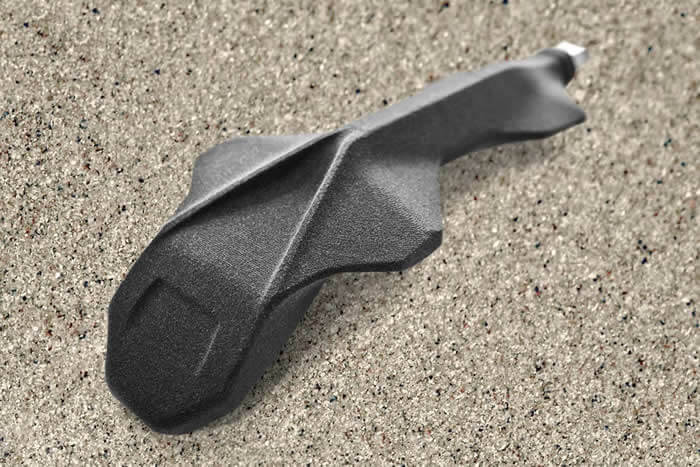
El Instituto de Construcción Aeronáutica de la Universidad de Stuttgart se encargó de colocar las fibras mediante la tecnología de trenzado. Para ello, el núcleo se fijó en un dispositivo de sujeción en la robótica de la instalación de trenzado y, por medio de la ruta de trenzado calculada en la simulación, se guió por la rueda de trenzado. Para el proyecto R.A.C.E. se utilizó un trenzador radial Herzog RF 1/64-100. La tela se colocó sobre el núcleo con 64 hilos de trenzado compuestos por hilos roving de fibra de carbono de 24 k. Qué tan fuerte se encuentra el trenzado sobre el núcleo, se determina por la fuerza de los resortes en los bolillos. 600 gramos de fuerza de tracción de los resortes suministra el mejor resultado de flexibilidad y resistencia para el trenzado biaxial.
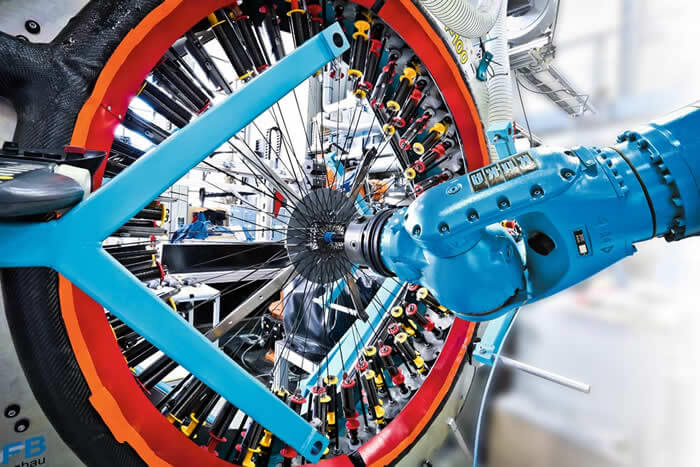
El sistema de poliuretano VITROX® RTM 332 de la empresa Huntsman utilizado para el soporte de matrícula de la Superduke 1290R destaca por sus excelentes características mecánicas y su capacidad de procesamiento. La alta resistencia al impacto y elasticidad del material cumplen con los requerimientos del componente. Las características de procesamiento son especialmente importantes para el proceso HP-RTM, ya que en la producción de serie cuenta el tiempo de ciclo. Con un tiempo "snap-cure" ajustable de menos de 30 segundos hasta 24 horas se pueden realizar también tiempos de ciclo más cortos con VITROX®.
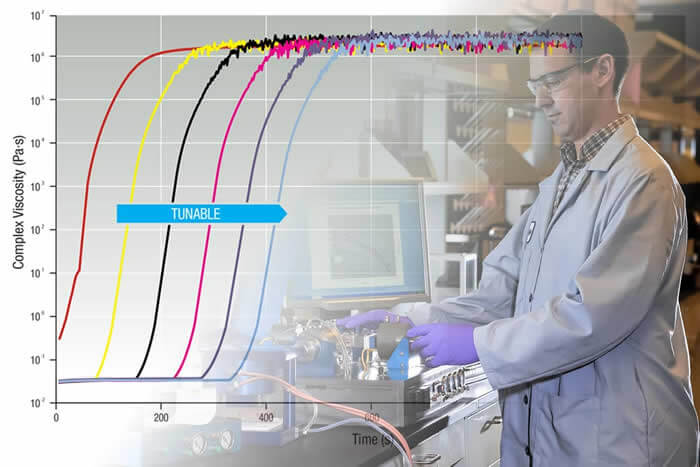
Un argumento especialmente decisivo para el uso del proceso HP-RTM es la alta calidad constante del componente. En el proyecto R.A.C.E., la planta incluye una máquina de dosificación de Hennecke del tipo STREAMLINE y una prensa de cierre vertical del tipo Engel elast 400V compact. Debido a la cooperación intensiva de las empresas Engel y Hennecke, se puede controlar todo el proceso a través de una planta. En el dispositivo de dosificación STREAMLINE se procesa tanto poliol como isocianato. Gracias al control de temperatura de toda la planta, incluidos los paquetes de manguera, se garantiza una temperatura constante mediante la recirculación de los componentes. Además, a través de un tercer hilo se puede inyectar un medio de separación homogeneizado.
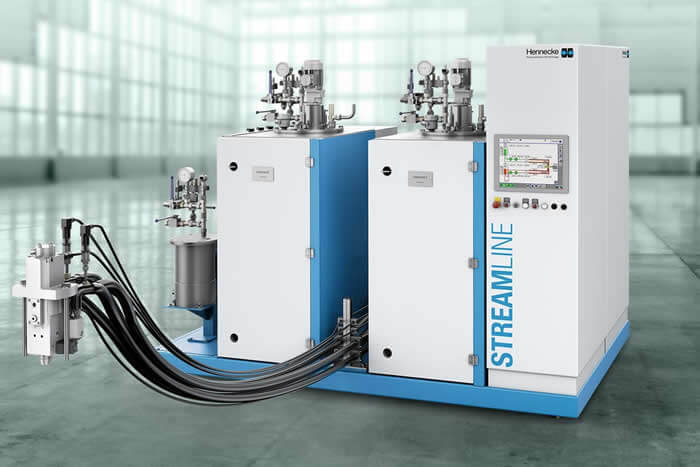
Para mezclar los componentes, Hennecke usa su cabezal de mezcla MN10-3 RTM actualmente desarrollado. Mediante el tubo de descarga cónico con el sensor de presión interna de molde integrado, se puede usar también el cabezal de mezcal de alta presión para los procesos de conexión semiautomáticos. Para contrarrestar la contracción durante la polimerización, el punzón autolimpiante ofrece además la función de presionar posteriormente para un control hidráulico durante el endurecimiento de la matriz. Así se pueden obtener la calidad más alta de las superficies. Una particularidad adicional del MN10-3 RTM es el montaje en serie con las boquillas de presión equilibrada patentadas. Así se evita por completo una posible influencia de la presión interna del molde sobre el proceso de presión de los componentes.
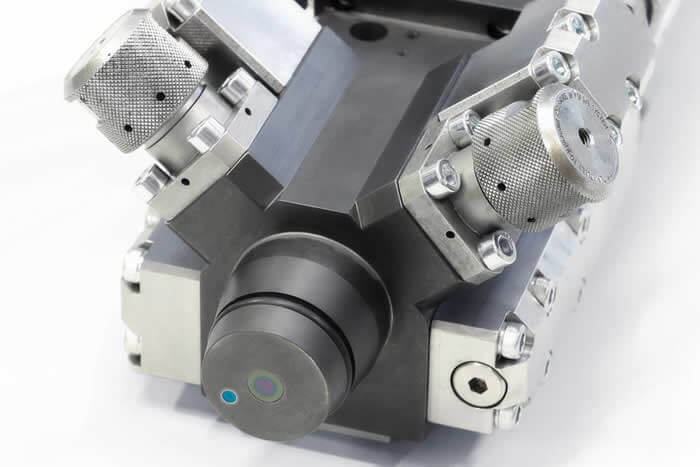
El uso de plásticos muy reactivos en presiones internas del molde hasta un máximo de 200 bar supone altas exigencias para la tecnología de moldes. Por una parte, el molde tiene que ofrecer una larga vida útil en el uso de las fibras de carbono abrasivas; por otra parte, tiene que garantizar una superficie constante bien pulida. Gracias a la experiencia del constructor de moldes Persico de Nembro, Italia, estas exigencias se pudieron cumplir con éxito en el proyecto R.A.C.E. En presiones internas de promedio del molde de alrededor de 100 bar, la junta también tiene que cumplir las altas exigencias. Para eso se usó un material sellante novedoso de la empresa Murtfeldt. Murlock®, un plástico termoplástico, ofrece un alto sellado en cientos de ciclos de proceso. En comparación con las juntas de cordel redondo usuales, el material es resistente a los daños por los materiales restantes o fibras de carbono, y también inerte químicamente en comparación con los sistemas de resina reactivos.
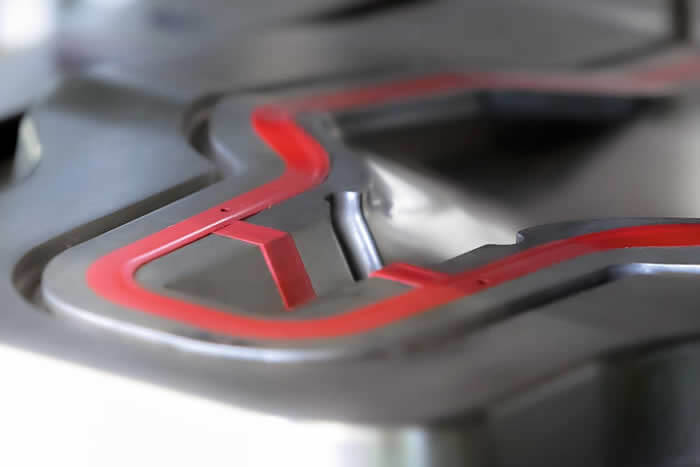
La activación del material nuclear mediante agua es algo muy especial de la tecnología CAVUS. Es tan especial porque los más importante es la sustentabilidad. El núcleo se puede despegar del componente sin disolventes contaminantes adicionales. Después de la separación del componente deformado en los bordes de corte, se introduce en agua. La arena se deposita en la solución y se puede usar otra vez para nuevos núcleos después del secado. El aglomerante que se encuentra en la solución se puede desechar como agua industrial o incluso se puede desprender y utilizarse como fertilizante para la agricultura. Después de retirar la arena del componente, se puede suministrar a los pasos usuales del procesamiento posterior de componentes de compuesto de fibra y luego instalarlo en el vehículo.
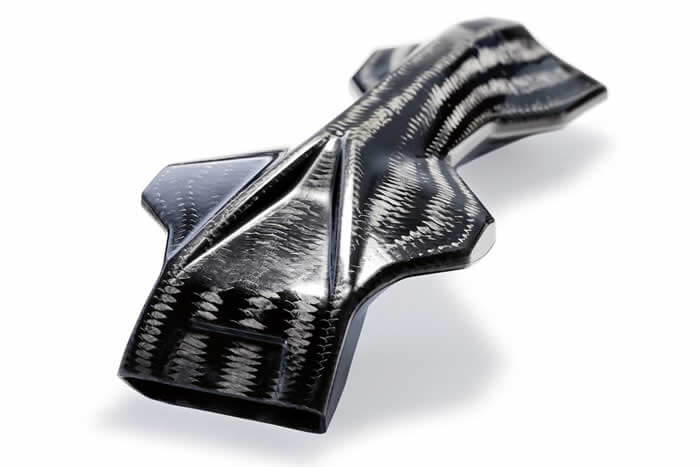
Testimonios de los socios del proyecto
Producción en vivo del componente en la feria K de Düsseldorf
Casi 4000 visitantes estuvieron en el stand de feria de Hennecke para ver el proceso. Un tiempo de ciclo Part-to-Part de 125 segundos y una reducción de peso de más del 62 por ciento con revalorización simultánea del producto son distintivos de un proyecto exitoso. Por eso, el proyecto R.A.C.E. demuestra de forma sorprendente cómo se puede alcanzar un desarrollo decisivo en el área de la fabricación en serie de componentes huecos de compuesto de fibra sobre la base de la tecnología CAVUS con los esfuerzos compartidos de los altamente especializados socios del proyecto.
Proyecto R.A.C.E. '2.0'
Soporte de matrícula en construcción híbrida (GFRP/CFRP)
El proyecto R.A.C.E. sigue en desarrollo constante. El nuevo inicio de producción es un soporte de matrícula en construcción híbrida que garantiza la máxima libertad de diseño a la hora de proporcionar forma y color. En el diseño de contorno en el proceso de trenzado se realiza con fibra de vidrio. Gracias a un refuerzo específico y por tanto apto para la carga mediante las fibras de carbono en el proceso Tailored-Fibre-Placement (TFP), el usuario recibe un componente que obtiene valores máximos de rigidez con muy poco peso y costos de materias primas muy reducidos. Además, un sellado del núcleo mejorado una vez más reduce la cantidad de fases necesarias del proceso, lo que minimiza de forma adicional los costos de producción. Asimismo, el nuevo inicio de producción permite la integración sencilla de los componentes electrónicos, como p. ej. sensores o diodos luminosos.
Aquí encontrará información complementaria en formato PDF
Para leer los documentos necesita Adobe Reader®, que puede ser descargado gratuitamente aquí.