PANELMASTER STEEL
The specific energy demand of residential and industrial buildings can be significantly reduced with modern insulation. It is not without reason that numerous governmental and non-governmental organizations are striving to establish sustainable measures in the construction and modernization of buildings. From an economic and environmental point of view, sandwich panel construction is much more than just an alternative to conventional building methods. The boom in the use of sandwich panels can be traced back to the energy crisis and the subsequent rapid increase in energy prices. Over the past five decades, the number of buildings constructed with sandwich panels has grown tremendously. Sandwich panels have long since become the standard choice for efficiently insulating building facades.
With its highly developed, continuously or discontinuously operating sandwich panel lines, Hennecke-OMS has played a decisive role in this success story right from the start. The new generation of PANELMASTER STEEL plants from Hennecke-OMS is the ideal system solution for the continuous production of high-quality steel sandwich panels with different rigid facings, thicknesses and profiles and the option of a core structure made of polyurethane or mineral wool. With a production capacity of up to 2.000.000 square meters per year, the advanced plant concept covers a wide range of applications. Users are impressed by the ease of operation and the helpful support systems.
The continuous production line
- Seamless, fully integrated production solution from a single source
- Smooth operation due to harmonized software controls across the production line
- Comprehensive worldwide training and service support for the complete production line
MINIMUM PRODUCTION HALL DIMENSIONS:
140 m x 35 m x 8 m (L x W x H)
AVERAGE PRODUCTIVITY:
1.300.000 - 2.000.000 m2 / year
LINE SPEED:
up to 15 m / min
Profiling
The profiling section contains the equipment for handling the coil and processing the metal facings. This includes unwinding and feeding the steel coils into the plant, preparing the strips by trimming and connecting them, as well as the profiling of the lower and upper metal facings. The surface and edge profiling gives the sandwich composite elements a defined shape and joins them securely together.
The profiling section usually consists of the following units:
- Facing infeed
- Lining
- Advanced profiling machines
- Additional equipment
Center section
The center section for continuous metal facings is the heart of each PANELMASTER STEEL production line.
It represents the accumulated know-how of our company in the processing of polyurethane under high pressure and usually consists of the following units:
- Pre-heating and primer unit
- Metering units
- Temperature and mass flow control units
- Static mixers and gas loading system
- Mixhead
- Foaming portal and laydown table
- Double belt laminator
- Tank farm
- Mineral wool (MIWO) infeed / supply of mineral wool plates
Outfeed section
The outfeed section begins by cutting the panels to the desired length and smoothly handling them to prepare the panel packages for shipping.
The PANELMASTER STEEL outfeed section typically includes the following units:
- Band saw
- Cooling unit
- Milling unit
- Stacking and turning unit
- EPS protection infeed unit
- Wrapping machine
Plant control system
The PANELMASTER STEEL automation system uses only high quality control components specifically designed for high performance sandwich panel production. The use of advanced, computerized electronic systems ensures maximum operational reliability and facilitates fast, largely automated product changes.
The intuitive visualization supports the operator in managing these tasks.
- Plant control
- Panel management system
- Process data acquisition and analysis
What are the features of sandwich panels?
Sandwich panels are special insulating boards composed of several sandwich-like layers. The structure usually consists of two facings, either rigid (steel plate) or flexible (aluminum foil or paper), and a core of polyurethane (PU/PIR) or mineral wool that acts as an insulating layer. Due to these composite layers, which are securely bonded together, the panels are also known as composite panels. Sandwich panels are comparatively lightweight yet have excellent mechanical properties, offering high rigidity and large support widths. This makes them easy to handle and assemble, and ensures low operating costs while maintaining high profitability. One of the most important features of the sandwich panel is its high level of thermal insulation, with a thermal conductivity of only 0.02 to 0.035 W/mk. In addition, the advanced components meet all major standards for residential and commercial use.
MATERIAL THICKNESS WITH THE SAME THERMAL INSULATION VALUE
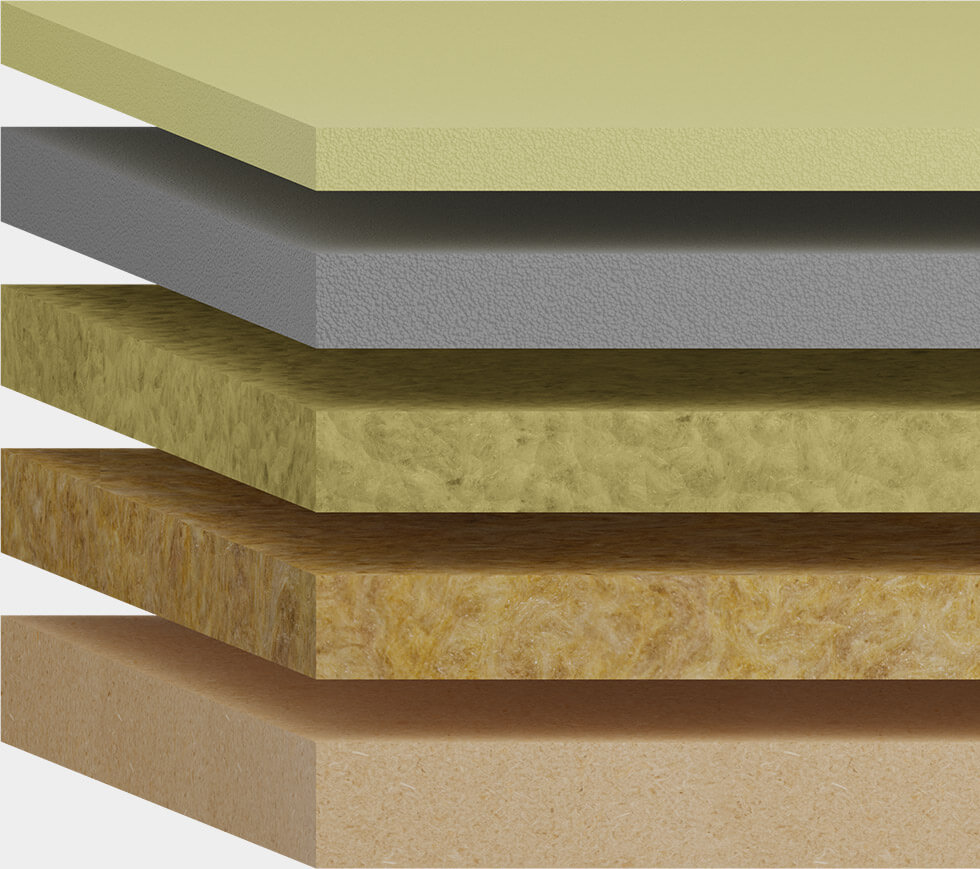
SANDWICH PANEL COMPOSITION
Facing
- Enhanced mechanical stability due to profiling (such as trapezoidal or wave profile)
- Ribs are used to increase mechanical stability (e.g. in roof panels)
- Coating ensures high resistance against environmental impacts (such as corrosion or scratch marks)
- Painting and sheet forming (such as lining, embosser) to achieve desired coloring and surface effects
- Use of all common steel plates for rigid facings
- Use of all common aluminium plates or kraft paper for flexible facings
Core structure
- Provides a solid connection to the facings and largely defines the panel thickness
- Defines the compressive strength and shear stiffness of the panel
- Polyurethane (PUR / PIR) or mineral wool are used
- The use of additives extends the range of applications (for example for fire protection
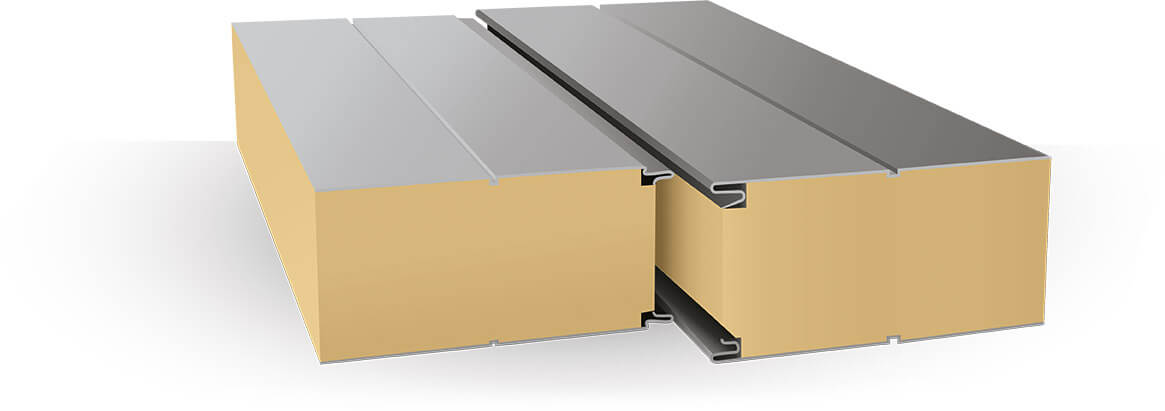
Dimensions and specs
Panel thickness: | 20 - 300 mm |
Panel length: | 2.000 - 18.000 mm |
Panel width: | 600 - 1.200 mm (standard is 1.000 mm) |
Facing steel thickness: | 0.4 - 0.8 mm |
PIR-PUR foam density: | 35 - 42 kg/m3 |
Where are sandwich panels used?
Sandwich panels with rigid facings are mainly used in the construction of halls, industrial buildings, cold and deep-freeze warehouses, as well as office and residential buildings. In addition to speeding up construction time and bringing significant cost savings, the use of sandwich panels has other advantages for architects: today, a whole new generation of sandwich panels meets not only structural and financial requirements, but also individual design needs. There are several types of rigid faced sandwich panels: Optionally, the multifunctional Hennecke-OMS system technology also enables product combinations of rigid and flexible facings. These panels are used, for example, in the agricultural sector.
Typical panel types
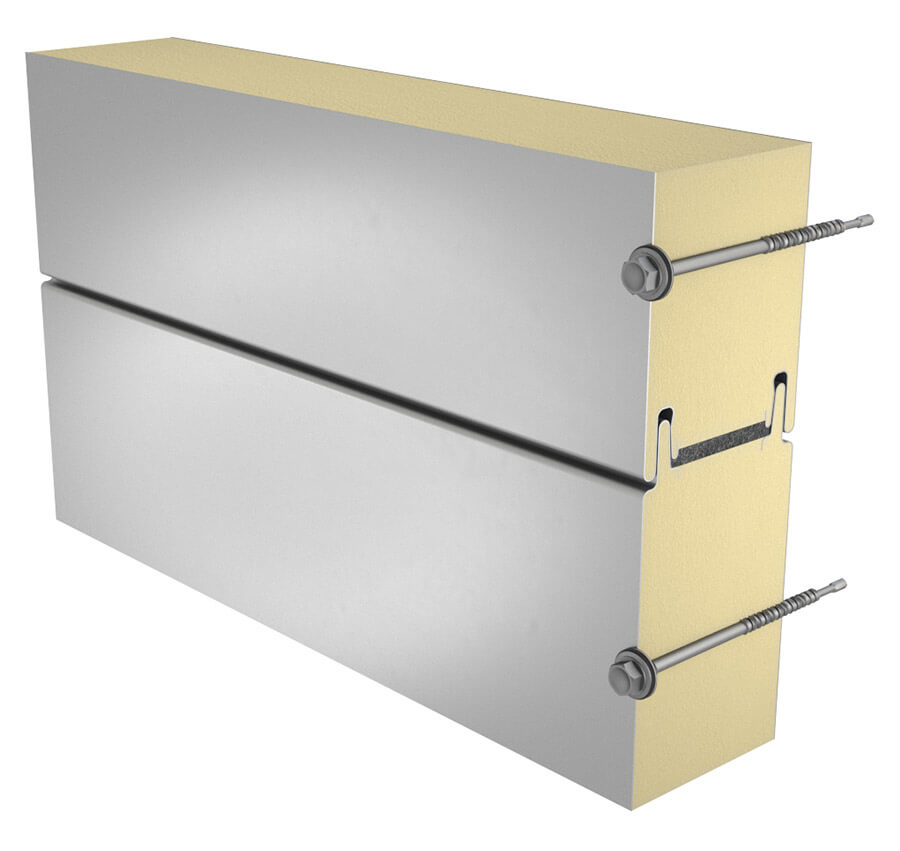
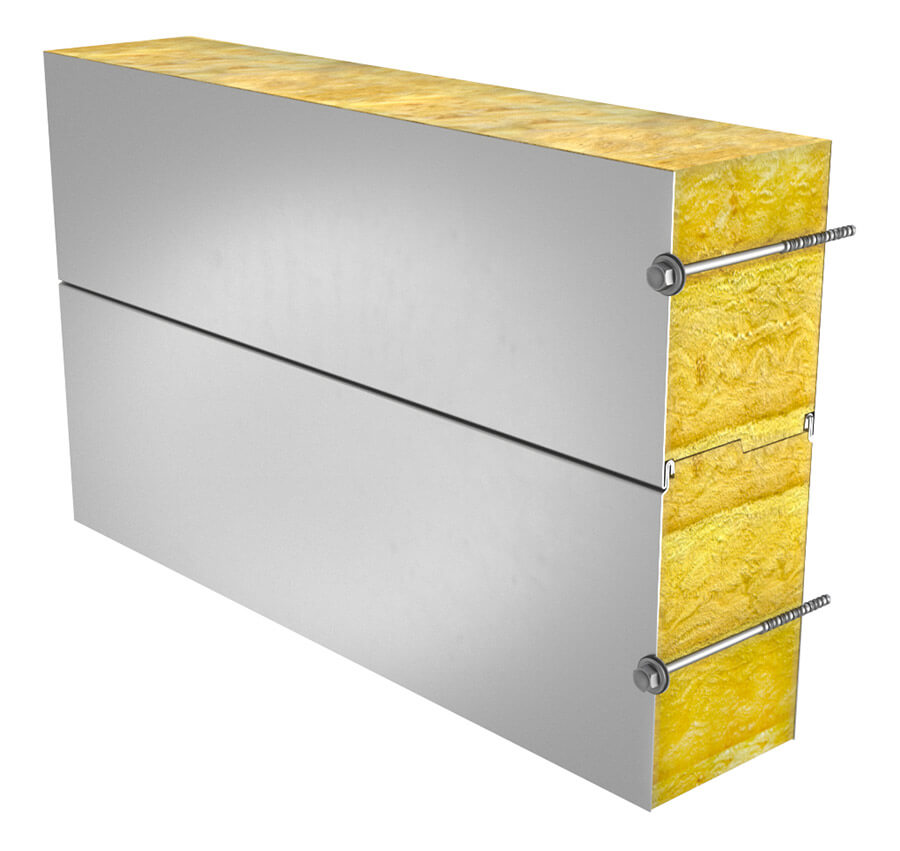
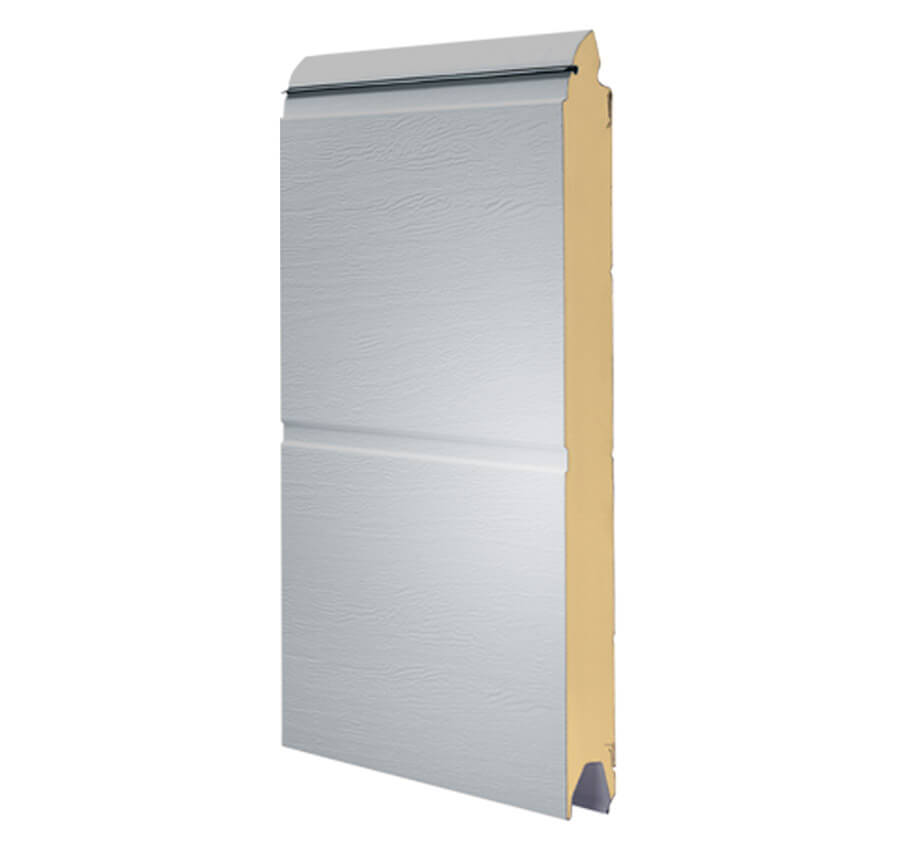
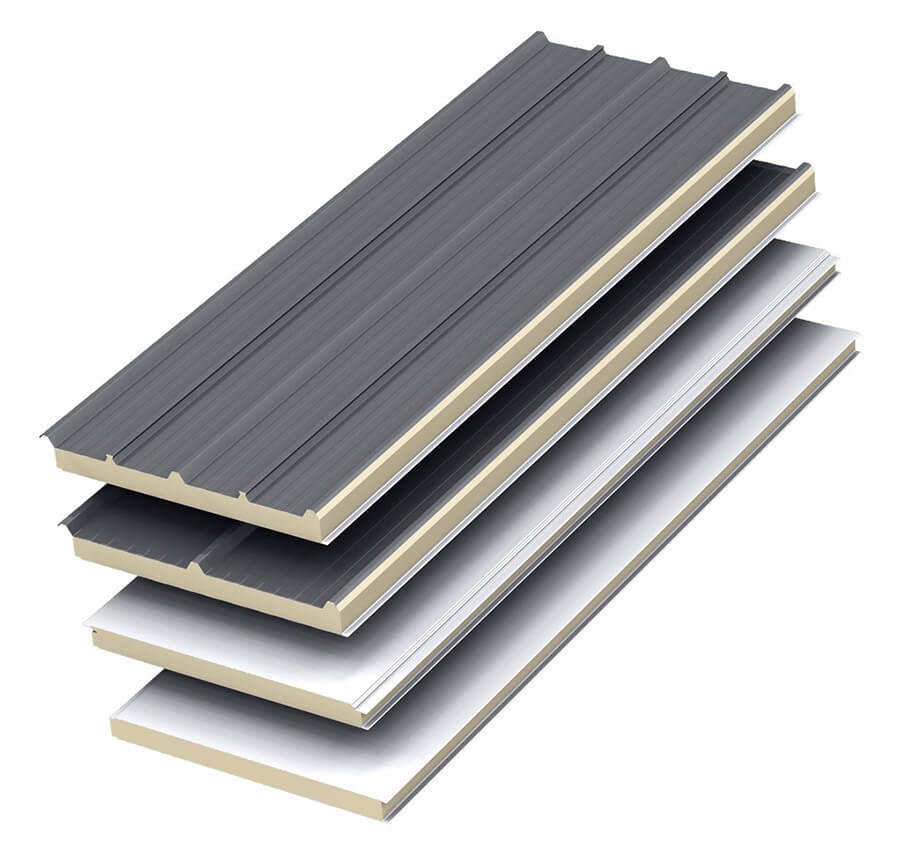
Click here for accompanying documents in the PDF format
You will need Adobe® Reader® that you can download here for free.